Physics:Stress triaxiality
In continuum mechanics, stress triaxiality is the relative degree of hydrostatic stress in a given stress state.[1] It is often used as a triaxiality factor, T.F, which is the ratio of the hydrostatic stress,
Stress triaxiality has important applications in fracture mechanics and can often be used to predict the type of fracture (i.e. ductile or brittle) within the region defined by that stress state. A higher stress triaxiality corresponds to a stress state which is primarily hydrostatic rather than deviatoric. High stress triaxiality (> 2–3) promotes brittle cleavage fracture[3] as well as dimple formation within an otherwise ductile fracture.[1][5] Low stress triaxiality corresponds with shear slip and therefore larger ductility,[5] as well as typically resulting in greater toughness.[6] Ductile crack propagation is also influenced by stress triaxiality, with lower values producing steeper crack resistance curves.[7] Several failure models such as the Johnson-Cook (J-C) fracture criterion (often used for high strain rate behavior),[8] Rice-Tracey model, and J-Q large scale yielding model incorporate stress triaxiality.
History
In 1959 Davies and Connelly introduced so called triaxiality factor, defined as the ratio of Cauchy stress first principal invariant divided by effective stress
Davies and Conelly were motivated in this proposal by supposition, correct in view of their own and later research, that negative pressure (spherical tension)
Wierzbicki and collaborators adopted a slightly modified definition of triaxiality factor than the original one
The name triaxiality factor is rather unfortunate, inadequate, because in physical terms the triaxiality factor determines the calibrated ratio of pressure forces relative to shearing forces or the ratio of isotropic (spherical) part of stress tensor in relation to its anisotropic (deviatoric) part both expressed in terms of their moduli,
The triaxiality factor does not discern triaxial stress states from states of lower dimension.
Ziółkowski proposed to use as a measure of pressure towards shearing forces another modification of the index
Stress Triaxiality factor in biaxial tests
The triaxiality factor
The class of biaxial tests is defined by the condition that always one of the principal values of the stress tensor is equal to zero (
The normalized third invariant of stress deviator is defined as
In presentation of material testing results, the most frequently at present, it is used so called Lode angle
Ziółkowski proposed to use a skewness angle

In micromechanical context the skewness angle can be understood as a macroscopic measure of the magnitude of internal entropy of the (macroscopic) Cauchy stress tensor. In this sense that its value determines degree of order of the population of micro pure shears (directional dipoles) generating the specific macroscopic stress state. The smaller is absolute values of skewness angle the smaller is internal entropy of Cauchy stress tensor.
The skewness angle enters as a parameter in a measure of anisotropy factor (degree) of stress tensor, which can be expressed with the formula
The
The isotropy angle enables extraction of the spherical (isotropic) part and deviatoric (anisotropic) part of the stress tensor in a very straightforward and convenient manner.
The measure of tensor anisotropy
The
A very simple (linear) connection exists between Lode angle and skewness angle
The Wierzbicki's constraint relation
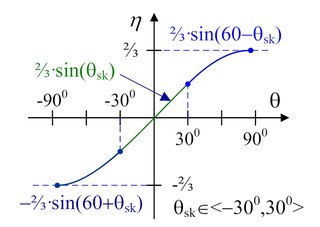
The above relations
The relations
Theorem I. The radial lines (rays) coming out from the origin
Theorem II. The relations
Corollary. In the case of convex critical surface, with the aid of any type of biaxial (plane) stress test, for any fixed value of mean stress (pressure)

In the case of convex critical surface, with the aid of any type of biaxial (plane) stress test, for any fixed value of skewness (Lode) angle
The Corrollary indicates for limitations of the class of biaxial (plane) tests in experimental examination of the influence of skewness (Lode) angle and pressure on materials behavior submitted to multiaxial loadings. This is so, because upon executing only biaxial tests no adequate experimental data results can be collected to reliably separate the influence of mean stress and/or skewness angle on the possible variations of critical effective stresses. One value of skewness angle for any fixed pressure and/or three values of pressure for any fixed skewness angle deliver skimpy information for such purpose.
Triaxialy factor as convenient indicator showing transition from two-dimensional (plane) stress to full three-dimensional state of stress
Relations
References
- ↑ Jump up to: 1.0 1.1 Fracture mechanics : twenty-fourth volume. Landes, J. D. (John D.), McCabe, Donald E., Boulet, Joseph Adrien Marie., ASTM Committee E-8 on Fatigue and Fracture., National Symposium on Fracture Mechanics (24th : 1992 : Gatlinburg, Tenn.). Philadelphia. pp. 89. ISBN 0-8031-1990-9. OCLC 32296916.
- ↑ Hancock, J.W.; Mackenzie, A.C. (June 1976). "On the mechanisms of ductile failure in high-strength steels subjected to multi-axial stress-states" (in en). Journal of the Mechanics and Physics of Solids 24 (2-3): 147–160. doi:10.1016/0022-5096(76)90024-7. https://linkinghub.elsevier.com/retrieve/pii/0022509676900247.
- ↑ Jump up to: 3.0 3.1 Soboyejo, W. O. (2003). "12.4.2 Cleavage Fracture". Mechanical properties of engineered materials. Marcel Dekker. ISBN 0-8247-8900-8. OCLC 300921090.
- ↑ Lemaitre, Jean (1992) (in en). A Course on Damage Mechanics. Berlin, Heidelberg: Springer Berlin Heidelberg. pp. 45. doi:10.1007/978-3-662-02761-5. ISBN 978-3-662-02763-9. http://link.springer.com/10.1007/978-3-662-02761-5.
- ↑ Jump up to: 5.0 5.1 Affonso, Luiz Octavio Amaral. (2013). Machinery Failure Analysis Handbook : Sustain Your Operations and Maximize Uptime.. Elsevier Science. pp. 33–42. ISBN 978-0-12-799982-1. OCLC 880756612.
- ↑ Anderson, T. L. (Ted L.), 1957- (1995). Fracture mechanics : fundamentals and applications (2nd ed.). Boca Raton: CRC Press. pp. 87. ISBN 0-8493-4260-0. OCLC 31514487.
- ↑ Dowling, N. E., Piascik, R. S., Newman, J. C. (1997). Fatigue and Fracture Mechanics: 27th Volume. United States: ASTM. (pp.75)
- ↑ International Symposium on Ballistics (29th : 2016 : Edinburgh, Scotland), author. (2016). Proceedings 29th International Symposium on Ballistics : Edinburgh, Scotland, UK, 9-13 May 2016. pp. 1136–1137. ISBN 978-1-5231-1636-2. OCLC 1088722637.
- ↑ Davies, E.A.; Connelly, F.M. (1959). "Stress distribution and plastic deformation in rotating cylinders of strain-hardening material". Journal of Applied Mechanics 26 (1): 25–30. doi:10.1115/1.4011918. Bibcode: 1959JAM....26...25D.
- ↑ Jump up to: 10.0 10.1 10.2 Wierzbicki, T.; Bao, Y.; Lee, Y-W.; Bai, Y. (2005). "Calibration and evaluation of seven fracture models". International Journal of Mechanical Sciences 47 (4–5): 719–743. doi:10.1016/j.ijmecsci.2005.03.003.
- ↑ Jump up to: 11.0 11.1 11.2 11.3 11.4 11.5 11.6 11.7 11.8 Ziółkowski, A.G. (2022). "Parametrization of Cauchy Stress Tensor Treated as Autonomous Object Using Isotropy Angle and Skewness Angle". Engineering Transactions 70 (2): 239–286. https://et.ippt.gov.pl/index.php/et/article/view/2210..
- ↑ Rychlewski, J. (1985). "Zur Abschätzung der Anisotropie (To estimate the anisotropy)". Journal of Applied Mathematics and Mechanics 65 (6): 256–258. doi:10.1002/zamm.19850650617. https://engrxiv.org/preprint/view/1359/.
![]() | Original source: https://en.wikipedia.org/wiki/Stress triaxiality.
Read more |