Engineering:Nanogenerator
A nanogenerator is a compact device that converts mechanical or thermal energy into electricity, serving as an energy harvesting solution for small, wireless autonomous devices. It taps into ambient energy sources like solar, wind, thermal differentials, and kinetic energy, enabling power generation for applications such as wearable electronics and wireless sensor networks. Nanogenerators utilize ambient background energy readily available in the environment, such as temperature gradients from machinery operation, electromagnetic energy in urban areas, or even motion vibrations during activities like walking. This approach offers a means to power low-energy electronics without the need for conventional fuel sources.
There are three classes of nanogenerators: piezoelectric, triboelectric, both of which convert mechanical energy into electricity, and pyroelectric nanogenerators, which convert heat energy into electricity.[1]
Piezoelectric nanogenerator
A piezoelectric nanogenerator is an energy-harvesting device capable of converting external kinetic energy into electrical energy via action by a nano-structured piezoelectric material. It is generally used to indicate kinetic energy harvesting devices utilizing nano-scaled piezoelectric material, like in thin-film bulk acoustic resonators.[2][3]
Mechanism
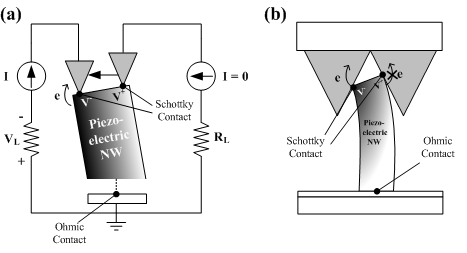
The working principle of the nanogenerator will be explained in two different cases: the force exerted perpendicular to and parallel to the axis of the nanowire.[4]
The working principle for the first case is explained by a vertically grown nanowire subjected to a laterally moving tip. When a piezoelectric structure is subjected to the external force of the moving tip, deformation occurs throughout the structure. The piezoelectric effect will create an electrical field inside the nanostructure; the stretched part with the positive strain will exhibit positive electrical potential, whereas the compressed part with negative strain will show the negative electrical potential. This is due to the relative displacement of cations with respect to anions in their crystalline structure. As a result, the tip of the nanowire will have an electrical potential distribution on its surface, while the bottom of the nanowire is neutralized since it is grounded. The maximum voltage generated in the nanowire can be calculated using the following equation:[5][math]\displaystyle{ V_{\text{max}} = \pm \frac{3}{4(\kappa_0+\kappa)}[e_{\text{33}} - 2(1 + \nu) e_{\text{15}} - 2\nu e_{\text{31}}] \frac{a^3}{l^3} \nu_{\text{max}}, }[/math]where κ0 is the permittivity in vacuum, κ is the dielectric constant, e33, e15, and e31 are the piezoelectric coefficients, ν is the Poisson ratio, a is the radius of the nanowire, l is the length of the nanowire, and νmax is the maximum deflection of the nanowire's tip.
The electrical contact plays an important role in pumping out charges on the surface of the tip. The Schottky contact must be formed between the counter electrode and the tip of the nanowire since the ohmic contact will neutralize the electrical field generated at the tip. In order to form an effective Schottky contact, the electron affinity (Ea) must be smaller than the work function (φ) of the metal composing the counter electrode. In the case of the ZnO nanowire with an electron affinity of 4.5 eV, Pt (φ = 6.1 eV) is a suitable metal to construct the Schottky contact. By constructing the Schottky contact, the electrons will pass to the counter electrode from the surface of the tip when the counter electrode is in contact with the regions of the negative potential, whereas no current will be generated when it is in contact with the regions of the positive potential, in the case of the n-type semiconductive nanostructure (the p-type semiconductive structure will exhibit the reversed phenomenon since the hole is mobile in this case).
For the second case, a model with a vertically grown nanowire stacked between the ohmic contact at its bottom and the Schottky contact at its top is considered. When the force is applied toward the tip of the nanowire, the uniaxial compressive force is generated in the nanowire. Due to the piezoelectric effect, the tip of the nanowire will have a negative piezoelectric potential, increasing the Fermi level at the tip. Since the electrons will then flow from the tip to the bottom through the external circuit, positive electrical potential will be generated at the tip. The Schottky contact will stop electrons from being transported through the interface, therefore maintaining the potential at the tip. As the force is removed, the piezoelectric effect diminishes, and the electrons will be flowing back to the top in order to neutralize the positive potential at the tip. The second case will generate an alternating current output signal.[6]
Geometrical configuration
Depending on the configuration of the piezoelectric nanostructure, the nanogenerator can be categorized into 3 types: VING, LING, and "NEG." Still, there is a configuration that does not fall into the aforementioned categories, as stated in other types.
Vertical nanowire Integrated Nanogenerator (VING).
VING is a 3-dimensional configuration consisting of a stack of 3 layers, which are the base electrode, the vertically grown piezoelectric nanostructure, and the counter electrode. The piezoelectric nanostructure is usually grown on the base electrode, which is then integrated with the counter electrode in full or partial mechanical contact with its tip.
The first VING was in 2007[7] with a counter electrode with the periodic surface grating resembling the arrays of the AFM tip as a moving electrode. Since the counter electrode is not in full contact with the tips of the piezoelectric nanowire, its motion in-plane or out-of-plane caused by the external vibration induces the deformation of the piezoelectric nanostructure, leading to the generation of the electrical potential distribution inside each individual nanowire. The counter electrode is coated with metal, forming a schottky contact with the tip of the nanowire, where only the compressed portion of the piezoelectric nanowire would allow the accumulated electrons to pass through the barrier between its tip and the counter electrode, in the case of the n-type nanowire. The switch-on and-off characteristic of this configuration shows its capability of generating direct current without any requirement for the external rectifier.
In VING with partial contact, the geometry of the counter electrode plays an important role. The flat counter electrode would not induce sufficient deformation of the piezoelectric nanostructures, especially when the counter electrode moves in in-plane mode. After the basic geometry resembling the array of AFM tips, a few other approaches have been followed for facile development of the counter electrode. Professor Zhong Lin Wang's group has generated counter electrodes composed of ZnO nanorods, utilizing a similar technique used for synthesizing ZnO nanowire arrays. Professor Sang-Woo Kim's group at Sungkyunkwan University (SKKU) and Dr. Jae-Young Choi's group at Samsung Advanced Institute of Technology (SAIT) in South Korea introduced a bowl-shaped transparent counter electrode by combining anodized aluminum and electroplating technology.[8] They have also developed the other type of counter electrode by using networked single-walled carbon nanotube (SWNT) on the flexible substrate, which is not only effective for energy conversion but also transparent.[9]
The other type of VING has also been suggested. While it shares the identical geometric configuration as the aforementioned, such a VING has full mechanical contact between the tips of the nanowires and the counter electrode.[10]
Lateral nanowire Integrated Nanogenerator (LING).
LING is a 2-dimensional configuration consisting of three parts: the base electrode, the laterally grown piezoelectric nanostructure, and the metal electrode for schottky contact. In most cases, the thickness of the substrate film is much thicker than the diameter of the piezoelectric nanostructure, so the individual nanostructure is subjected to a pure tensile strain. A
LING is an expansion of the single wire generator (SWG), where a laterally aligned nanowire is integrated on the flexible substrate.
LING generates an AC electrical signal. The output voltage increased, resulting in an array of LING connected in series on the single substrate, leading to the constructive addition of the output voltage. Such a configuration may lead to the practical application of LING for scavenging large-scale power, for example, wind or ocean waves.
Nanocomposite Electrical Generators (NEG).
"NEG" is a 3-dimensional configuration consisting of three main parts: the metal plate electrodes, the vertically grown piezoelectric nanostructure, and the polymer matrix, which fills in between the piezoelectric nanostructure.
NEG was introduced by Momeni et al.[11] It was shown that NEG has a higher efficiency compared to the original nanogenerator configuration, in which a ZnO nanowire will be bended by an AFM tip. It is also shown that it provides an energy source with higher sustainability.
Other type. A fabric-like geometrical configuration has been suggested where a piezoelectric nanowire is grown vertically on the two microfibers in their radial direction, and they are twined to form a nanogenerator.[12] One of the microfibers is coated with the metal to form a schottky contact, serving as the counter electrode for VINGs. As the movable microfiber is stretched, the deformation of the nanostructure occurs on the stationary microfiber, resulting in voltage generation. Its working principle is identical to that of VINGs with partial mechanical contact, thus generating a DC electrical signal.
Materials
Among the various piezoelectric materials studied for the nanogenerator, much of the research has focused on materials with a wurtzite structure, such as ZnO, CdS[13] and GaN.[14] An attempt to enhance the piezoelectricity of the individual nanowire also led to the development of other piezoelectric materials based on Wurtzite structures. Professor Zhong Lin Wang of the Georgia Institute of Technology introduced p-type ZnO nanowires.[15] Unlike the n-type semiconductive nanostructure, the mobile particle in the p-type is a hole, thus the schottky behavior is reversed from that of the n-type case; the electrical signal is generated from the portion of the nanostructure where the holes are accumulated. It has been shown experimentally that p-type Z nOnanowirese can generate an output signal that is nearly 10 times that of n-type ZnOnanowirese.
From the idea that the material with a perovskite structure is known to have more effective piezoelectric characteristics compared to that with a wurtzite structure, barium titanate (BaTiO3) nanowire has also been studied by Professor Min-Feng Yu of the University of Illinois at Urbana-Champaign.[16] The output signal is found to be more than 16 times that of a similar ZnO nanowire.
Professor Liwei Lin of the University of California, Berkeley, has suggested that PVDF can also be applied to form a nanogenerator.[17] The nanofiber can be directly written on the substrate controlling the process, and this technique is expected to be applied for forming self-powered textiles based on nanofiber. Researchers from SUTD presented the successful synthesis of ultra-long potassium niobate (KNbO3) nanofibers using a sol-gel-assisted far-field electrospinning process[18] and utilized them to develop a high-output voltage flexible nanogenerator.[19]
Considering that the piezoelectric constant plays a critical role in the overall performance of a piezoelectric nanogenerator, another research direction to improve device efficiency is to find new materials with a large piezoelectric response. Lead Magnesium Niobate-Lead Titanate (PMN-PT) is a next-generation piezoelectric material with a super-high piezoelectric constant when ideal composition and orientation are obtained. In 2012, PMN-PT nanowires with a very high piezoelectric constant were fabricated by a hydrothermal approach[20] and then assembled into an energy-harvesting device.[21] The record-high piezoelectric constant was further improved by the fabrication of a single-crystal PMN-PT nanobelt,[22] which was then used as the essential building block for a piezoelectric nanogenerator.
A comparison of the reported materials as of 2010 is given in the following table.
Material | Type | Geometry | Output voltage | Output power | Synthesis | Researched at |
---|---|---|---|---|---|---|
ZnO (n-type) | Wurtzite | D: ~100 nm, L: 200~500 nm | VP=~9 mV @ R=500 MΩ | ~0.5 pW per cycle (estimated) | CVD, hydrothermal process | Georgia Tech. |
ZnO (p-type) | Wurtzite | D: ~50 nm, L: ~600 nm | VP=50~90 mV @ R=500 MΩ | 5~16.2 pW per cycle (calculated) | CVD | Georgia Tech. |
ZnO-ZnS | Wurtzite (Heterostructure) | Not stated | VP=~6 mV @ R=500 MΩ | ~0.1 pW per cycle (calculated) | Thermal evaporation and etching | Georgia Tech. |
GaN | Wurtzite | D: 25~70 nm, L: 10~20 μm | Vavg=~20 mV, Vmax=~0.35 V@ R=500 MΩ | ~0.8 pW per cycle (average, calculated) | CVD | Georgia Tech.[23] |
CdS | Wurtzite | D: ~100 nm, L: 1 μm | VP=~3 mV | Not stated | PVD, Hydrothermal Process | Georgia Tech.[24] |
BaTiO3 | Perovskite | D: ~280 nm, L: ~15 μm | VP=~25 mV @ R=100 MΩ | ~0.3 aJ per cycle (stated) | High temperature chemical reaction | UIUC[25] |
PVDF | Polymer | D: 0.5~6.5 μm, L: 0.1~0.6 mm | VP=5~30 mV | 2.5 pW~90 pW per cycle (calculated) | Electro spinning | UC Berkeley[17] |
KNbO3 | Perovskite | D: ~100 nm; L: few cm | Vp = ~16 V @ R=100 MΩ | Electro spinning | SUTD/MIT[19] |
Applications
Energy harvesting by nanogenerators is expected to be applied to underutilized energy sources such as solar, wind, thermal, pressure, human power, vibrations, etc.
Self-powered nano/micro devices. One of the feasible applications of nanogenerators is as an independent or supplementary energy source for nano/microdevices that consume relatively little energy in a condition where the kinetic energy is supplied continuously. One example was introduced by Professor Zhong Lin Wang's group in 2010 by the self-powered pH or UV sensor integrated VING with an output voltage of 20~40mV onto the sensor.
Still, the converted electrical energy is relatively small for operating nano/micro devices; therefore, the range of its application is still limited as a supplementary energy source to the battery. The breakthrough is being sought by combining the nanogenerator with other types of energy harvesting devices, such as solar cells or biochemical energy harvesters.[26][27] This approach is expected to contribute to the development of an energy source suitable for applications where independent operation is crucial, such as Smartdust.
Smart wearable systems The outfit integrated or made of the textiles with the piezoelectric fiber is one of the feasible applications of the nanogenerator. The kinetic energy from the human body is converted to electrical energy through the piezoelectric fibers, and it can possibly be applied to supply portable electronic devices such as health-monitoring systems attached to smart wearable systems. Nanogenerators such as VING can also be easily integrated into the shoe by employing the walking motion of the human body.
Another similar application is a power-generating artificial skin. Professor Zhong Lin Wang's group has shown the possibility by generating an AC voltage of up to 100 mV from the flexible SWG attached to the running hamster.[28]
Transparent and flexible devices. Some of the piezoelectric nanostructure can be formed on various kinds of substrates, such as flexible and transparent organic substrates. The research groups in SKKU (Professor Sang-Woo Kim's group) and SAIT (Dr. Jae-Young Choi's group) have developed a transparent and flexible nanogenerator that can possibly be used for self-powered tactile sensors, and it is anticipated that the development may be extended to energy-efficient touch-screen devices. Their research focus is being extended to enhance the transparency of the device and its cost-effectiveness by substituting an indium-tin-oxide (ITO) electrode with a graphene layer.[29]
Implantable telemetric energy receiver. The nanogenerator based on ZnO nanowire can be applied to implantable devices since ZnO is not only biocompatible but can also be synthesized on the organic substrate, rendering the nanogenerator biocompatible overall. The implantable device integrated with the nanogenerator can be operated by receiving external ultrasonic vibration outside the human body, which is converted to electrical energy by the piezoelectric nanostructure.
Triboelectric nanogenerator
Overview
A triboelectric nanogenerator is an energy-harvesting device that converts mechanical energy into electricity using the triboelectric effect. They were first demonstrated in Prof. Zhong Lin Wang's group at Georgia Institute of Technology in 2012.[30][31] A potential is created by charge transfer between two thin organic or inorganic films and electron flow between two electrodes attached to the back sides of the film to balance the potential.
Ever since the first report of the TENG in January 2012, the output power density of the TENG has improved, reaching 313 W/m2, the volume density reaches 490 kW/m3, and conversion efficiencies of ~60%[32]–72%[33] have been demonstrated. This new energy technology also has a number of other advantages, such as low cost in manufacturing and fabrication, robustness and reliability, and environmental friendliness. The triboelectric nanogenerator can be applied to harvest all kinds of mechanical energy, such as human motion, walking, vibration, mechanical triggering, rotating tires, wind, flowing water, and more.[32]
Ramakrishna Podila's group at Clemson University demonstrated the first truly wireless triboelectric nanogenerators,[34] which were able to charge energy storage devices (e.g., batteries and capacitors) without the need for any external amplification or boosters.[35]
The triboelectric nanogenerator has three basic operation modes: vertical contact-separation mode, in-plane sliding mode, and single-electrode mode. They have different characteristics and are suitable for different applications.
Basic modes and mechanisms
Vertical Contact-Separation ModeFile:Vertical contact-separation mode of triboelectric nanogenerator.tif
The working mechanism of the triboelectric nanogenerator can be described as the periodic change of the potential difference induced by the cycled separation and re-contact of the opposite triboelectric charges on the inner surfaces of the two sheets. When a mechanical agitation is applied to the device to bend or press it, the inner surfaces of the two sheets will come into close contact, and the charge transfer will begin, leaving one side of the surface with positive charges and the other with negative charges. When the deformation is released, the two surfaces with opposite charges will separate automatically, so that these opposite triboelectric charges will generate an electric field and induce a potential difference across the top and bottom electrodes. In order to screen this potential difference, the electrons will flow from one electrode to the other through the external load. The electricity generated in this process will continue until the potentials of the two electrodes are the same. Subsequently, when the two sheets are pressed towards each other again, the triboelectric-charge-induced potential difference will begin to decrease to zero, so that the transferred charges will flow back through the external load to generate another current pulse in the opposite direction. When this periodic mechanical deformation lasts, the alternating current (AC) signals will be continuously generated.[36][37]
As for the pair of materials getting into contact and generating triboelectric charges, at least one of them needs to be an insulator so that the triboelectric charges cannot be conducted away but will remain on the inner surface of the sheet. Then, these immobile triboelectric charges can induce AC electricity flow in the external load under the periodic distance change.
Lateral Sliding ModeFile:Lateral sliding mode of triboelectric nanogenerator.tif
There are two basic friction processes: normal contact and lateral sliding. One TENG is designed based on the in-plane sliding between the two surfaces in a lateral direction.[38] With triboelectrification from sliding, a periodic change in the contact area between two surfaces leads to a lateral separation of the charge centers, which creates a voltage driving the flow of electrons in the external load. The measured curre is determined by the rate at which the two plates are being slid apart. Subsequently, when the top plate is reverted to slide backwards, the separated charges begin to get in contact again, but there is no annihilation due to the insulating nature of the polymer materials. The redundant transferred charges on the electrodes will flow back through the external load with the increase in contact area in order to maintain electrostatic equilibrium. This will contribute to a current flow from the bottom electrode to the top electrode, along with the second half cycle of sliding. Once the two plates reach the overlapping position, the charged surfaces come into full contact again. There will be no transferred charges left on the electrode, and the device returns to the first state. In this entire cycle, the processes of sliding outward and inward are symmetric, so a pair of symmetric alternating current peaks should be expected.
The mechanism of in-plane charge separation can work in either one-directional sliding between two plates[39] or in rotation mode.[40] In the sliding mode, introducing linear grating or circular segmentation on the sliding surfaces is an extremely efficient means for energy harvesting. With such structures, two patterned triboelectric surfaces can get to a fully mismatched position through a displacement of only a grating unit length rather than the entire length of the TENG, which dramatically increases the transport efficiency of the induced charges.
Single-Electrode Mode
A single-electrode-based triboelectric nanogenerator is introduced as a more practical and feasible design for some applications, such as fingertip-driven triboelectric nanogenerators.[41][42] The working principle of the single-electrode TENG is schematically shown in the figure by the coupling of contact electrification and electrostatic induction. In the original position, the surfaces of skin and PDMS fully contact each other, resulting in charge transfer between them. According to the triboelectric series, electrons were injected from the skin to the PDMS since the PDMS is more triboelectrically negative than the skin, which is a contact electrification process. The produced triboelectric charges with opposite polarities are fully balanced or screened, leading to no electron flow in the external circuit. Once a relative separation between PDMS and skin occurs, these triboelectric charges cannot be compensated. The negative charges on the surface of the PDMS can induce positive charges on the ITO electrode, driving free electrons to flow from the ITO electrode to ground. This electrostatic induction process can give an output voltage or current signal if the distance separating between the touching skin and the bottom PDMS is appreciably comparable to the size of the PDMS film. When negative triboelectric charges on the PDMS are fully screened from the induced positive charges on the ITO electrode by increasing the separation distance between the PDMS and skin, no output signals can be observed, as illustrated. Moreover, when the skin is reverted to approach the PDMS, the induced positive charges on the ITO electrode decrease, and the electrons will flow from ground to the ITO electrode until the skin and PDMS fully contact each other again, resulting in a reversed output voltage/current signal.
Applications
TENG is a physical process of converting mechanical agitation to an electric signal through triboelectrification (in the inner circuit) and electrostatic induction processes (in the outer circuit). This basic process has been demonstrated for energy harvesting and for a self-powered active sensor.
Harvesting vibration energy
Harvesting vibration energy might be used for powering mobile electronics, particularly in combination with complementary balanced energy harvesting techniques. Various applications of a triboelectric nanogenerator has been demonstrated in the following aspects: 1. The cantilever-based technique is a classical approach for harvesting mechanical energy, especially for MEMS. By designing the contact surface of a cantilever with the top and bottom surfaces during vibration, TENG has been demonstrated for harvesting ambient vibration energy based on the contact-separation mode.[43] 2. To harvest the energy from a backpack, we demonstrated a rationally designed TENG with integrated rhombic gridding, which greatly improved the total current output owing to the structurally multiplied unit cells connected in parallel.[44] 3. With the use of four supporting springs, a harmonic resonator-based TENG has been fabricated based on the resonance-induced contact separation between the two triboelectric materials, which has been used to harvest vibration energy from an automobile, a sofa, and a desk.[45] 4. Recently, a three-dimensional triboelectric nanogenerator (3D-TENG) has been designed based on a hybridization mode of conjunction between the vertical contact-separation mode and the in-plane sliding mode. The innovative design facilitates harvesting random vibration energy in multiple directions over a wide bandwidth. The 3-D TENG is designed for harvesting ambient vibration energy, especially at low frequencies.
Harvesting environmental energy
A triboelectric nanogenerator is an ideal energy harvester that can collect diverse mechanical energies from the environment, especially low-frequency mechanical energies like wind and water waves. In 2013, Zhonglin Wang's group reported a rotary triboelectric nanogenerator for harvesting wind energy.[46] Subsequently, various types of triboelectric nanogenerators for harvesting ambient energy have been proposed, like 3D spiral structure triboelectric nanogenerators to collect wave energy,[47] fully enclosed triboelectric nanogenerators applied in water and harsh environments[48] and multi-layered disk nanogenerators for harvesting hydropower.[49] However, due to the limitations of the nanogenerator's working models, the friction generated between layers of the triboelectric nanogenerator will inevitably reduce the energy conversion efficiency and the durability of the device. This defect hinders the further application of friction nanogenerators in the field of environmental energy collection. Zhonglin Wang's group tried to fabricate a frictionless electrostatic induction nanogenerator circulation network to overcome the "friction" problem.[50] In their tests, this frictionless electrostatic induction nanogenerator exhibited high energy converting efficiency and excellent durability. Circulation networks composed of such frictionless nanogenerators could be used to harvest water wave energy and continuously provide energy to some wireless devices.
Besides, some novel nanogenerators used for harvesting the droplet energy were reported. Researchers designed an all-weather droplet-based triboelectric nanogenerator, which relied on the contact electrification effect between liquid and solid to generate electricity.[51] The advantage of this liquid-solid model is that it effectively avoids the wear of nanogenerators. Yunlong Zi's group reported a hybrid cell combining a silicon solar cell with a water-droplet-harvesting triboelectric nanogenerator. This hybrid cell had the capacity to harvest both solar and raindrop energies.[52]
- Harvesting energy from human body motion
Triboelectric nanogenerator can be used to convert human body's mechanical energy into electricity for charging portable electronics and biomedical applications.[53] A packaged power-generating insole with built-in flexible multi-layered triboelectric nanogenerators has been demonstrated, which enable the harvesting of mechanical pressure during normal walking. The TENG used here relies on the contact-separation mode and is effective in responding to the periodic compression of the insole. A tug can be attached to the inner layer of a shirt for harvesting energy from body motion. The maximum output voltage and current density are up to 17V and 0.02μA/cm2, respectively. The TENG with a single layer size of 2 cm×7 cm×0.08 cm sticking on the clothes was demonstrated as a sustainable power source that not only can directly light up 30 light-emitting diodes (LEDs), but also can charge a lithium-ion battery by persistently clapping clothes.
- Self-powered active strain/force sensors
A triboelectric nanogenerator automatically generates an output voltage and current once it is mechanically triggered. The magnitude of the output signal signifies the impact of the mechanical deformation and its time-dependent behavior. This is the basic principle of the TENG, which can be applied as a self-powered pressure sensor. The voltage-output signal can reflect the applied pressure induced by a droplet of water. All types of TENGs have a high sensitivity and fast response to the external force and show a sharp peak signal. Furthermore, the response to the impact of a piece of feather (20 mg, ~0.4Pa in contact pressure) can be detected. The sensor signal can delicately show these details of the entire process. The existing results show that our sensor can be used for measuring subtle pressure in real life.[54]
The active pressure sensor has also been developed in the form of a composite. The term "triboelectric composite" refers to a sponge-shaped polymer with embedded wire. Applying pressure and impact on the composite in any direction causes charge separation between the soft polymer and the active wire because of the presence of a composite air gap. Passive wire as the second electrode may be either embedded inside the sponge without any air gap or placed out of the composite, allowing the sensor to work in single-electrode mode.[55]
In the case where we make a matrix array of the triboelectric nanogenerators, a large-area, self-powered pressure map applied to a surface can be realized.[56] The response of the TENG array to local pressure was measured through a multi-channel measurement system. There are two types of output signals from the TENG: open-circuit voltage and short-circuit current. The open-circuit voltage is only dictated by the final configuration of the TENG after applying mechanical triggering, so it is a measure of the magnitude of the deformation, which is attributed to the static information to be provided by the TENG. The output current depends on the rate at which the induced charge would flow, so that the current signal is more sensitive to the dynamic process of how the mechanical triggering is applied.
The active pressure sensor and the integrated sensor array based on the triboelectric effect have several advantages over conventional passive pressure sensors. First, the active sensor is capable of both static pressure sensing using the open-circuit voltage and dynamic pressure sensing using the short-circuit current, while conventional sensors are usually incapable of dynamic sensing to provide loading rate information. Second, the prompt response of both static and dynamic sensing enables the revealing of details about the loading pressure. Third, the detection limit of the TENG for dynamic sensing is as low as 2.1Pa, owing to the high output of the TENG. Fourth, the active sensor array presented in this work has no power consumption and could even be combined with its energy harvesting functionality for self-powered pressure mapping. Future works in this field involve the miniaturization of the pixel size to achieve higher spatial resolution and the integration of the TEAS matrix onto a fully flexible substrate for shape-adaptive pressure imaging.
- Self-powered motion sensors
The term "self-powered sensors" can refer to a system that powers all the electronics responsible for measuring and demonstrating detectable movement. For example, the self-powered triboelectric encoder, integrated into a smart belt-pulley system, converts friction into useful electrical energy by storing the harvested energy in a capacitor and fully powering the circuit, which includes a microcontroller and an LCD.[57]
- Self-powered active chemical sensors
As for triboelectric nanogenerators, maximizing the charge generation on opposite sides can be achieved by selecting the materials with the largest difference in the ability to attract electrons and changing the surface morphology. In such a case, the output of the TENG depends on the type and concentration of molecules adsorbed on the surface of the triboelectric materials, which can be used for fabricating chemical and biochemical sensors. As an example, the performance of the TENG depends on the assembly of Au nanoparticles (NPs) onto the metal plate. These assembled Au NPs not only act as steady gaps between the two plates in strain-free conditions but also enable the function of enlarging the contact area of the two plates, which will increase the electrical output of the TENG. Through further modification of 3-mercaptopropionic acid (3-MPA) molecules on the assembled Au NPs, the high-output nanogenerator can become a highly sensitive and selective nanosensor toward Hg2+ ion detection because of the different triboelectric polarities of Au NPs and Hg2+ ions. With its high sensitivity, selectivity, and simplicity, the TENG holds great potential for the determination of Hg2+ ions in environmental samples. As different ions, molecules, and materials have their own unique triboelectric polarities, we expect that the TENG can become either an electrical turn-on or turn-off sensor when the analytes are selectively bound to the modified electrode surface. Some believe that this work will serve as the stepping stone for related TENG studies and inspire the development of TENG toward other metal ions and biomolecules such as DNA and proteins in the near future.[58]
Choice of materials and surface structures
Almost all materials known exhibit the triboelectrification effect, from metal to polymer to silk to wood—almost everything. All of these materials can be candidates for fabricating TENGs, so the material choices for TENG are huge. However, the ability of a material to gain or lose an electron depends on its polarity. John Carl Wilcke published the first triboelectric series in 1757 on static charges. A material towards the bottom of the series, when touched by a material near the top of the series, will attain a more negative charge. The further away two materials are from each other on the series, the greater the charge transferred.
The surfaces of the materials can be functionalized chemically using various molecules, nanotubes, nanowires, or nanoparticles in order to enhance the triboelectrification effect.
Besides these pure materials, the contact materials can be made of composites, such as nanoparticles embedded in the polymer matrix. This not only changes the surface electrification but also the permittivity of the materials for electrostatic induction.
Standards and Figures-of-Merit
A performance figure-of-merit (FOMP) has been developed to quantitatively evaluate the performance of triboelectric nanogenerators, consisting of a structural figure-of-merit (FOMS) related to the structure of TENG and a material figure-of-merit (FOMM) that is the square of the surface charge density.[59] Considering the breakdown effect, a revised figure-of-merit is also proposed.[60] Based on the FOM, the outputs of different TENGs can be compared and evaluated.
- Cycles for energy output of TENG
For a continuous periodic mechanical motion (from displacement x=0 to x=xmax), the electrical output signal from the TENG is also periodically time-dependent. In such a case, the average output power P, which is related to the load resistance, is used to determine the merits of the TENG. Given a certain period of time T, the output energy per cycle E can be derived as: [math]\displaystyle{ E=PT=\int VI\, dt= \oint V\,dQ }[/math]
This indicates that the output energy per cycle E can be calculated as the encircled area of the closed loop in the V-Q curve, and all V-Q cycles are named "cycles for energy output" (CEO).
- Cycles for maximized energy output of TENG.
By periodic transformation between in load and short circuit conditions, cycles for maximum energy output can be obtained. When the load equals infinite, the V-Q becomes a trapezoid shape, the vertices of which are determined by the maximum short-circuit transferred charge QSC,max, and the maximum output energy can be calculated as:[math]\displaystyle{ E_{\text{m}}=\frac{1}{2} Q_{\text{SC,max}}(V_{\text{OC,max}} +V_{\text{OC}}\prime) }[/math]
- Figures-of-merit (FOM) of TENG.
For the TENG operating in CMEO with infinite load resistance, the period T includes two parts of time. One part is from the relative motion in TENG, and the other part is from the discharging process in short-circuit conditions. The breakdown effect is widely present in triboelectric nanogenerators, which will seriously affect the effective maximum energy output, Eem.[61] Therefore, the average output power P at CMEO considering the breakdown effect should satisfy:[math]\displaystyle{ P=\frac{E_{\text{em}}}{T}\approx \frac{E_{\text{em}}}{\frac{2x_{\text{max}}}{v}} = \frac{v}{2} \frac{E_{\text{em}}}{x_{\text{max}}} }[/math]Where v is the average velocity value of the relative motion in TENG, which depends on the input mechanical motions. In this equation, [math]\displaystyle{ \frac{E_{\text{em}}}{x_{\text{max}}} }[/math] is the only term that depends on the characteristics of the TENG itself. The energy-conversion efficiency of the TENG can be expressed as (at CMEO with R=∞ considering breakdown effects):[math]\displaystyle{ yita=\frac{ E_{\text{out}} }{ E_{\text{in}} }= \frac{ E_{\text{output per cycle}} }{ E_{\text{output per cycle}}+ E_{\text{dissipation per cycle}}}}=\frac{1}{1+\frac{1}{\frac{E_{\text{em}}}{2Fx_{\text{max}}}} }[/math]Here F stands for the average dissipative force during the operation of the TENG.[62] This force can be frictional force, air resistance force or others. stands for the average dissipative force during the operation of the TENG. This force can be frictional force, air resistance force or others. Therefore, it can be concluded that the term [math]\displaystyle{ \frac{E_{\text{em}}}{x_{\text{max}}} }[/math] determines both the average power and the energy-conversion efficiency from the characteristics of TENG itself. Eem contains QSC,max that is proportional to the triboelectrification area A. Therefore, to exclude the effect of the TENG size on the output energy, the area A should be placed in denominator of this term and then the term [math]\displaystyle{ \frac{E_{\text{em}}}{Ax_{\text{max}}} }[/math] determines the merits of TENG. QSC,max, VOC,max and V max' are all proportional to the surface charge density σ. Therefore, Eem is proportional to the square of the surface charge density σ. Then, a dimensionless structural FOM (FOMS) of TENG can be defined, as the factor only depends on the structural parameters and xmax:[math]\displaystyle{ FOM_{\text{S}}=2\epsilon_0/\sigma^2 \frac{E_{\text{em}}}{Ax_{\text{max}}} }[/math]Here ε0 is the permittivity of the vacuum. This structural FOM represents the merit of the TENG from the structural design. And then the performance FOM (FOMP) of TENG can be defined as:[math]\displaystyle{ FOM_{\text{P}}=2\epsilon_0 \frac{E_{\text{em}}}{Ax_{\text{max}}} }[/math]Here,
[math]\displaystyle{ FOM_{\text{M}}=\sigma^2 }[/math]which is the only component related to the material properties. The FOMP can be considered the universal standard to evaluate varieties of TENGs since it is directly proportional to the greatest possible average output power and related to the highest achievable energy conversion efficiency, regardless of the mode and the size of the TENG.
Standardized Method for Output Capacity Assessment
With the breakdown effect considered, a standardized method is proposed for output capability assessment of nanogenerators, which can experimentally measure the breakdown limit and Eem of nanogenerators.[60] Former studies on the theoretical model imply that TENG can be considered a voltage source combining with a capacitor in series, of which the capacitance varies during operation.[63] Based on the capacitive property, the assessment method is developed by charging the target TENG (TENG1) at different displacements x to measure the breakdown condition. Another TENG (TENG2) is added as the high-voltage source to trigger the target TENG to approach the breakdown condition. Switch 1 (S1) and switch 2 (S2) are used to enable different measurement steps. Detailed process flow of this method, including an experiment part and a data analysis part First of all, it is critical to keep the surface charge density identical as reflected by QSC,max, to ensure the consistency of measurement at different x. Thus, in Step 1, S1 was turned on and S2 was turned off to measure QSC,max; if QSC,max is lower than the expected value, an additional triboelectrification process is conducted to approach that. And then in Step 2, x was set to a certain value, and the short-circuit charge transfer QSC(x) at a certain x was measured by the coulometer Q1. In step 3, S1 was turned off, S2 was turned on, and then TENG2 was triggered to supply high-voltage output for TENG1. The charge flowing into TENG1 and the voltage across TENG1 were measured at the same time, in which the charge was measured by coulometer Q2, and the voltage was obtained by multiplying the resistance R with the current flowing through it as measured by current meter I, as detailed in Methods. The turning points obtained in this case (Q, V) were considered the breakdown points. And then, if x<xmax, the process was repeated starting from step 1 with an increased x until xmax was achieved to finish the experimental measurement part. For the data analysis part, first, C(x) was calculated from the slope of the linear part in the measured (Q, V) by considering it as the non-breakdown part. And then, the first turning point (Qb(x), Vb(x)) was determined at the variant R2 value by linearly fitting C(x), which was considered the threshold breakdown point. Finally, for any x∈[0, xmax], all the (Qb(x), Vb(x)) can be transferred into (QSC(x)-Qb(x), Vb(x)) as the breakdown points plotted in the V-Q cycle to calculate the Eem of TENG.
File:DC-TENG.tif Direct current triboelectric nanogenerator based on electrostatic breakdown
The direct current triboelectric nanogenerator (DC-TENG) is a new-type triboelectric nanogenerator that can harvest mechanical energy and convert it into electrical energy through the combination of the triboelectric effect and the electrostatic breakdown effect.[64][65] Different from the above-mentioned traditional triboelectric nanogenerators possessing a standard AC output signal, in which the signal is generated by a combination of triboelectric effect and electrostatic induction effect, the DC-TENG produces a unidirectional current flow in the external circuit and can drive electronic devices and charge energy storage devices directly. When the direct current triboelectric nanogenerator is fabricated in a rotary structure, it will produce continuous constant current, which can be utilized as a constant current power supply over a wide range of external load resistances. This new-type triboelectric nanogenerator was first invented by the Profs. Zhong Lin Wang and Jie Wang group at the Beijing Institute of Nanoenergy and Nanosystems in 2019. As a device for converting mechanical energy into electrical energy, this new-type triboelectric nanogenerator can be utilized in micro/nano power sources or self-power sensing systems.
Mechanism
The working mechanism of a direct current triboelectric nanogenerator is the coupling between contact electrification and electrostatic breakdown effects. Its conventional structure is quite simple, consisting of a friction electrode that is used for contact electrification with a friction layer and a charge-collecting electrode that collects the charges formed by electrostatic breakdown. During the sliding process, the friction electrode contacts the friction layer, resulting in positive charges on the friction electrode and negative charges on the friction layer due to the contact electrification. Due to the existence of charges on the friction layer, with the device sliding further, the gap between the charge-collecting electrode and friction layer will build a strong electric field, which will lead to an air breakdown in the gap and generate direct current in the external circuit if the electric field is strong enough. When the direct current triboelectric nanogenerator device slides to the end of the friction layer film, the air breakdown process will stop.
Pyroelectric nanogenerator
A pyroelectric nanogenerator is an energy-harvesting device that converts external thermal energy into electrical energy by using nano-structured pyroelectric materials. Usually, harvesting thermoelectric energy mainly relies on the Seebeck effect, which utilizes a temperature difference between two ends of the device to drive the diffusion of charge carriers.[66] However, in an environment where the temperature is spatially uniform without a gradient, such as in the outdoors, the Seebeck effect cannot be used to harvest thermal energy from a time-dependent temperature fluctuation. In this case, the pyroelectric effect has to be the choice, which is about the spontaneous polarization in certain anisotropic solids as a result of temperature fluctuation.[67] The first pyroelectric nanogenerator was introduced by Prof. Zhong Lin Wang at the Georgia Institute of Technology in 2012.[68] By harvesting the waste heat energy, this new type of nanogenerator has potential applications such as wireless sensors, temperature imaging, medical diagnostics, and personal electronics.
Mechanism

The working principle of a pyroelectric nanogenerator will be explained in two different cases: the primary pyroelectric effect and the secondary pyroelectric effect.
The working principle for the first case is explained by the primary pyroelectric effect, which describes the charge produced in a strain-free case. The primary pyroelectric effect dominates the pyroelectric response in PZT, BTO, and some other ferroelectric materials.[69] The mechanism is based on the thermally induced random wobbling of the electric dipole around its equilibrium axis, the magnitude of which increases with increasing temperature.[70] Due to thermal fluctuations at room temperature, the electric dipoles will randomly oscillate within a degree from their respective aligning axes. Under a fixed temperature, the total average strength of the spontaneous polarization from the electric dipoles is constant, resulting in no output from the pyroelectric nanogenerator. If we apply a change in temperature in the nanogenerator from room temperature to a higher temperature, the increase in temperature will result in the electric dipoles oscillating within a larger degree of spread around their respective aligning axes. The total average spontaneous polarization decreases due to the spread of the oscillation angles. The quantity of induced charges in the electrodes is thus reduced, resulting in a flow of electrons. If the nanogenerator is cooled instead of heated, the spontaneous polarization will be enhanced since the electric dipoles oscillate within a smaller degree of spread angle due to the lower thermal activity. The total magnitude of the polarization is increased, and the amount of induced charges in the electrodes is also increased. The electrons will then flow in the opposite direction.
In the second case, the obtained pyroelectric response is explained by the secondary pyroelectric effect, which describes the charge produced by the strain induced by thermal expansion. The secondary pyroelectric effect dominates the pyroelectric response in ZnO, CdS, and some other wurzite-type materials. The thermal deformation can induce a piezoelectric potential difference across the material, which can drive the electrons to flow in the external circuit. The output of the nanogenerator is associated with the piezoelectric coefficient and the thermal deformation of the materials. The output current I of the pyroelectric nanogenerators can be determined by the equation I=pA(dT/dt), where p is the pyroelectric coefficient, A is the effective area of the NG, and dT/dt is the rate of change in temperature.
Applications
Pyroelectric nanogenerators are expected[by whom?] to be applied for various applications where time-dependent temperature fluctuations exist. One of the feasible applications of the pyroelectric nanogenerator is as an active sensor, which can work without a battery. One example has been introduced by Professor Zhong Lin Wang's group in 2012 by using a pyroelectric nanogenerator as a self-powered temperature sensor for detecting a change in temperature, where the response time and reset time of the sensor are about 0.9 and 3 s, respectively.[71]
See also
- Battery (electricity)
- Electrical generator
- Microelectromechanical Systems
- Micropower
- Nanoelectromechanical systems
- Smartdust
- Smart Wearable Systems
References
- ↑ Sripadmanabhan Indira, Sridhar; Aravind Vaithilingam, Chockalingam; Oruganti, Kameswara Satya Prakash; Mohd, Faizal; Rahman, Saidur (May 20, 2019). "Nanogenerators as a Sustainable Power Source: State of Art, Applications, and Challenges" (in en). Nanomaterials 9 (5): 773. doi:10.3390/nano9050773. ISSN 2079-4991. PMID 31137520.
- ↑ Wang, Z. L.; Song, J. (June 2006). "Piezoelectric Nanogenerators Based on Zinc Oxide Nanowire Arrays". Science 312 (5771): 242–246. doi:10.1126/science.1124005. PMID 16614215. Bibcode: 2006Sci...312..242W. http://www.nanoscience.gatech.edu/zlwang/paper/2006/06_SCIENCE_1.pdf.
- ↑ Zhao, X.; et, al (May 2021). "Hybridized nanogenerators for effectively scavenging mechanical and solar energies". Science 24 (5): 102415. doi:10.1016/j.isci.2021.102415. PMID 33997695. Bibcode: 2021iSci...24j2415Z.
- ↑ M, Ani Melfa Roji; G, Jiji; T, Ajith Bosco Raj (2017-06-29). "A retrospect on the role of piezoelectric nanogenerators in the development of the green world" (in en). RSC Advances 7 (53): 33642–33670. doi:10.1039/C7RA05256A. ISSN 2046-2069. Bibcode: 2017RSCAd...733642R. https://pubs.rsc.org/en/content/articlelanding/2017/ra/c7ra05256a.
- ↑ Wang, Zhong Lin; Wang, Xudong; Song, Jinhui; Liu, Jin; Gao, Yifan (2008). "Piezoelectric Nanogenerators for Self-Powered Nanodevices". IEEE Pervasive Computing 7 (1): 49–55. doi:10.1109/mprv.2008.14. http://www.nanoscience.gatech.edu/zlwang/paper/2008/08_PVC_1.pdf. Retrieved 2012-06-15.
- ↑ Wang, Zhong Lin; Song, Jinhui (2006-04-14). "Piezoelectric Nanogenerators Based on Zinc Oxide Nanowire Arrays" (in en). Science 312 (5771): 242–246. doi:10.1126/science.1124005. ISSN 0036-8075. PMID 16614215. Bibcode: 2006Sci...312..242W. https://www.science.org/doi/10.1126/science.1124005.
- ↑ Wang, Xudong; Song, Jinhui; Liu, Jin; Wang, Zhong Lin (2007). "Direct-Current Nanogenerator Driven by Ultrasonic Waves". Science 316 (5821): 102–105. doi:10.1126/science.1139366. PMID 17412957. Bibcode: 2007Sci...316..102W. http://www.nanoscience.gatech.edu/zlwang/paper/2007/07_SCI_1.pdf.
- ↑ Choi, M. Y.; Choi, D.; Jin, M. J.; Kim, I.; Kim, S. H.; Choi, J. Y.; Lee, S. Y.; Kim, J. M. et al. (5 June 2009). "Mechanically Powered Transparent Flexible Charge-Generating Nanodevices with Piezoelectric ZnO Nanorods". Advanced Materials 21 (21): 2185–2189. doi:10.1002/adma.200803605. Bibcode: 2009AdM....21.2185C. http://home.skku.edu/~nesel/bbs/paper%20files/68.pdf.
- ↑ Choi, D.; Choi, M. Y.; Shin, H. J.; Yoon, S. M.; Seo, J. S.; Choi, J. Y.; Lee, S. Y.; Kim, J. M. et al. (2010). "Nanoscale Networked Single-Walled Carbon-Nanotube Electrodes for Transparent Flexible Nanogenerators". Journal of Physical Chemistry C 114 (2): 1379–1384. doi:10.1021/jp909713c. http://dchoi.khu.ac.kr/2010%2001%2012%20papers/09~10/2010_JPCC_NanoScaleNetwork.pdf.
- ↑ Xu, Sheng; Qin, Yong; Xu, Chen; Wei, Yaguang; Yang, Rusen; Wang, Zhong Lin (2010). "Self-powered nanowire devices". Nature Nanotechnology 5 (5): 366–373. doi:10.1038/nnano.2010.46. PMID 20348913. Bibcode: 2010NatNa...5..366X. http://www.nanoscience.gatech.edu/zlwang/paper/2010/10_NN_01.pdf.
- ↑ Momeni, K.; Odegard, G. M.; Yassar, R. S. (2010). "Nanocomposite electrical generator based on piezoelectric zinc oxide nanowires". Journal of Applied Physics 108 (11): 114303–114303–7. doi:10.1063/1.3517095. Bibcode: 2010JAP...108k4303M. http://www.me.mtu.edu/~reza/index_files/JAPpiezo.pdf.
- ↑ Qin, Yong; Wang, Xudong; Wang, Zhong Lin (14 February 2008). "Microfibre–nanowire hybrid structure for energy scavenging". Nature 451 (7180): 809–813. doi:10.1038/nature06601. PMID 18273015. Bibcode: 2008Natur.451..809Q. http://nanoscience.gatech.edu/paper/2008/08_nat_1.pdf.
- corrected in Qin, Yong; Wang, Xudong; Wang, Zhong Lin (15 January 2009). "Microfibre–nanowire hybrid structure for energy scavenging". Nature 457 (7227): 340. doi:10.1038/nature07628. Bibcode: 2009Natur.457..340Q.
- ↑ Lin, Y.-F.; Song, J.; Ding, Y.; Lu, S.-Y.; Wang, Z. L. (14 January 2008). "Piezoelectric nanogenerator using CdS nanowires". Applied Physics Letters 92 (2): 022105. doi:10.1063/1.2831901. Bibcode: 2008ApPhL..92b2105L. http://www.nanoscience.gatech.edu/zlwang/paper/2008/08_APL_1.pdf.
- ↑ Huang, Chi-Te; Song, Jinhui; Lee, Wei-Fan; Ding, Yong; Gao, Zhiyuan; Hao, Yue; Chen, Lih-Juann; Wang, Zhong Lin (7 April 2010). "GaN Nanowire Arrays for High-Output Nanogenerators". Journal of the American Chemical Society 132 (13): 4766–4771. doi:10.1021/ja909863a. PMID 20218713. http://www.nanoscience.gatech.edu/zlwang/paper/2010/10_JACS_01.pdf.
- ↑ Lu, M. P.; Song, J.; Lu, M. Y.; Chen, M. T.; Gao, Y.; Chen, L. J.; Wang, Z. L. (March 2009). "Piezoelectric Nanogenerator Using p-Type ZnO Nanowire Arrays". Nano Letters 9 (3): 1223–1227. doi:10.1021/nl900115y. PMID 19209870. Bibcode: 2009NanoL...9.1223L. http://nanoscience.gatech.edu/paper/2009/nano_lett_1223.pdf.
- ↑ Wang, Z.; Hu, J.; Suryavanshi, A. P.; Yum, K.; Yu, M. F. (October 2007). "Voltage Generation from Individual BaTiO3 Nanowires under Periodic Tensile Mechanical Load". Nano Letters 7 (10): 2966–2969. doi:10.1021/nl070814e. PMID 17894515. Bibcode: 2007NanoL...7.2966W. https://netfiles.uiuc.edu/mfyu/www/Documents/Publications/NL1-2007.pdf.
- ↑ Jump up to: 17.0 17.1 Chang, Chieh; Tran, Van H.; Wang, Junbo; Fuh, Yiin-Kuen; Lin, Liwei (10 February 2010). "Direct-Write Piezoelectric Polymeric Nanogenerator with High Energy Conversion Efficiency". Nano Letters 10 (2): 726–731. doi:10.1021/nl9040719. PMID 20099876. Bibcode: 2010NanoL..10..726C. http://www-bsac.eecs.berkeley.edu/publications/search/send_publication_pdf2client.php?pubID=1263244614.
- ↑ Ganeshkumar, Rajasekaran; Sopiha, Kostiantyn V; Wu, Ping; Cheah, Chin Wei; Zhao, Rong (2016-08-30). "Ferroelectric KNbO3nanofibers: synthesis, characterization and their application as a humidity nanosensor". Nanotechnology 27 (39): 395607. doi:10.1088/0957-4484/27/39/395607. ISSN 0957-4484. PMID 27573538. Bibcode: 2016Nanot..27M5607G.
- ↑ Jump up to: 19.0 19.1 Ganeshkumar, Rajasekaran; Cheah, Chin Wei; Xu, Ruize; Kim, Sang-Gook; Zhao, Rong (2017). "A high output voltage flexible piezoelectric nanogenerator using porous lead-free KNbO3 nanofibers". Applied Physics Letters 111 (1): 013905. doi:10.1063/1.4992786. Bibcode: 2017ApPhL.111a3905G.
- ↑ Xu, Shiyou; Poirier, Gerald; Yao, Nan (2012-05-09). "PMN-PT Nanowires with a Very High Piezoelectric Constant". Nano Letters 12 (5): 2238–2242. doi:10.1021/nl204334x. ISSN 1530-6984. PMID 22494473. Bibcode: 2012NanoL..12.2238X.
- ↑ Xu, Shiyou; Yeh, Yao-wen; Poirier, Gerald; McAlpine, Michael C.; Register, Richard A.; Yao, Nan (2013-06-12). "Flexible Piezoelectric PMN–PT Nanowire-Based Nanocomposite and Device". Nano Letters 13 (6): 2393–2398. doi:10.1021/nl400169t. ISSN 1530-6984. PMID 23634729. Bibcode: 2013NanoL..13.2393X.
- ↑ Wu, Fan; Cai, Wei; Yeh, Yao-Wen; Xu, Shiyou; Yao, Nan (2016-03-01). "Energy scavenging based on a single-crystal PMN-PT nanobelt" (in en). Scientific Reports 6: 22513. doi:10.1038/srep22513. ISSN 2045-2322. PMID 26928788. Bibcode: 2016NatSR...622513W.
- ↑ Huang, Chi-Te; Song, Jinhui; Lee, Wei-Fan; Ding, Yong; Gao, Zhiyuan; Hao, Yue; Chen, Lih-Juann; Wang, Zhong Lin (7 April 2010). "GaN Nanowire Arrays for High-Output Nanogenerators". Journal of the American Chemical Society 132 (13): 4766–4771. doi:10.1021/ja909863a. PMID 20218713. http://www.nanoscience.gatech.edu/zlwang/paper/2010/10_JACS_01.pdf.
- ↑ Lin, Y.-F.; Song, J.; Ding, Y.; Lu, S.-Y.; Wang, Z. L. (14 January 2008). "Piezoelectric nanogenerator using CdS nanowires". Applied Physics Letters 92 (2): 022105. doi:10.1063/1.2831901. Bibcode: 2008ApPhL..92b2105L. http://www.nanoscience.gatech.edu/zlwang/paper/2008/08_APL_1.pdf.
- ↑ Wang, Z.; Hu, J.; Suryavanshi, A. P.; Yum, K.; Yu, M. F. (October 2007). "Voltage Generation from Individual BaTiO3 Nanowires under Periodic Tensile Mechanical Load". Nano Letters 7 (10): 2966–2969. doi:10.1021/nl070814e. PMID 17894515. Bibcode: 2007NanoL...7.2966W. https://netfiles.uiuc.edu/mfyu/www/Documents/Publications/NL1-2007.pdf.
- ↑ Xu, Chen; Wang, Xudong; Wang, Zhong Lin (29 April 2009). "Nanowire Structured Hybrid Cell for Concurrently Scavenging Solar and Mechanical Energies". Journal of the American Chemical Society 131 (16): 5866–5872. doi:10.1021/ja810158x. PMID 19338339. http://finechem.dlut.edu.cn/matingli/pdf/Xu-2009-Nanowire%20Structured.pdf.
- ↑ Hansen, Benjamin J.; Liu, Ying; Yang, Rusen; Wang, Zhong Lin (27 July 2010). "Hybrid Nanogenerator for Concurrently Harvesting Biomechanical and Biochemical Energy". ACS Nano 4 (7): 3647–3652. doi:10.1021/nn100845b. PMID 20507155. http://nanoscience.gatech.edu/paper/2010/10_ACSN_02.pdf.
- ↑ Yang, R.; Qin, Y.; Li, C.; Zhu, G.; Wang, Z. L. (March 2009). "Converting Biomechanical Energy into Electricity by a Muscle-Movement-Driven Nanogenerator". Nano Letters 9 (3): 1201–1205. doi:10.1021/nl803904b. PMID 19203203. Bibcode: 2009NanoL...9.1201Y. http://nanoscience.gatech.edu/paper/2009/nano_lett_1201.pdf.
- ↑ Choi, Dukhyun; Choi, Min-Yeol; Choi, Won Mook; Shin, Hyeon-Jin; Park, Hyun-Kyu; Seo, Ju-Seok; Park, Jongbong; Yoon, Seon-Mi et al. (18 May 2010). "Fully Rollable Transparent Nanogenerators Based on Graphene Electrodes". Advanced Materials 22 (19): 2187–2192. doi:10.1002/adma.200903815. PMID 20376853. Bibcode: 2010AdM....22.2187C.
- ↑ Fan, F. R.; Tian, Z. Q.; Lin Wang, Z. (2012). "Flexible triboelectric generator". Nano Energy 1 (2): 328–334. doi:10.1016/j.nanoen.2012.01.004.
- ↑ Wang, Zhong, Lin (October 15, 2012). "Self-Powered Magnetic Sensor Based on a Triboelectric Nanogenerator". ACS Nano 6 (11): 10378–10383. doi:10.1021/nn304374m. PMID 23061926. https://pubs.acs.org/doi/epdf/10.1021/nn304374m.
- ↑ Jump up to: 32.0 32.1 Wang, Z. L. (2013). "Triboelectric Nanogenerators as New Energy Technology for Self-Powered Systems and as Active Mechanical and Chemical Sensors". ACS Nano 7 (11): 9533–9557. doi:10.1021/nn404614z. PMID 24079963.
- ↑ Xiong, Pu (25 September 2015). "Efficient Charging of Li-Ion Batteries with Pulsed Output Current of Triboelectric Nanogenerators". Advanced Science 3 (1): 1500255. doi:10.1002/advs.201500255. PMID 27774382.
- ↑ Pacha, Aswathi (2017-12-30). "Nanogenerators go wireless" (in en-IN). The Hindu. ISSN 0971-751X. https://www.thehindu.com/sci-tech/technology/nanogenerators-go-wireless/article22332379.ece.
- ↑ Mallineni, Sai Sunil Kumar; Dong, Yongchang; Behlow, Herbert; Rao, Apparao M.; Podila, Ramakrishna (2018). "A Wireless Triboelectric Nanogenerator" (in en). Advanced Energy Materials 8 (10): 1702736. doi:10.1002/aenm.201702736. ISSN 1614-6840.
- ↑ Zhu, G.; Pan, C.; Guo, W.; Chen, C. Y.; Zhou, Y.; Yu, R.; Wang, Z. L. (2012). "Triboelectric-Generator-Driven Pulse Electrodeposition for Micropatterning". Nano Letters 12 (9): 4960–4965. doi:10.1021/nl302560k. PMID 22889363. Bibcode: 2012NanoL..12.4960Z.
- ↑ Wang, S.; Lin, L.; Wang, Z. L. (2012). "Nanoscale Triboelectric-Effect-Enabled Energy Conversion for Sustainably Powering Portable Electronics". Nano Letters 12 (12): 6339–6346. doi:10.1021/nl303573d. PMID 23130843. Bibcode: 2012NanoL..12.6339W.
- ↑ Wang, S.; Lin, L.; Xie, Y.; Jing, Q.; Niu, S.; Wang, Z. L. (2013). "Sliding-Triboelectric Nanogenerators Based on In-Plane Charge-Separation Mechanism". Nano Letters 13 (5): 2226–2233. doi:10.1021/nl400738p. PMID 23581714. Bibcode: 2013NanoL..13.2226W.
- ↑ Zhu, G.; Chen, J.; Liu, Y.; Bai, P.; Zhou, Y. S.; Jing, Q.; Pan, C.; Wang, Z. L. (2013). "Linear-Grating Triboelectric Generator Based on Sliding Electrification". Nano Letters 13 (5): 2282–2289. doi:10.1021/nl4008985. PMID 23577639. Bibcode: 2013NanoL..13.2282Z.
- ↑ Lin, L.; Wang, S.; Xie, Y.; Jing, Q.; Niu, S.; Hu, Y.; Wang, Z. L. (2013). "Segmentally Structured Disk Triboelectric Nanogenerator for Harvesting Rotational Mechanical Energy". Nano Letters 13 (6): 2916–2923. doi:10.1021/nl4013002. PMID 23656350. Bibcode: 2013NanoL..13.2916L.
- ↑ Yang, Y.; Zhou, Y. S.; Zhang, H.; Liu, Y.; Lee, S.; Wang, Z. L. (2013). "A Single-Electrode Based Triboelectric Nanogenerator as Self-Powered Tracking System". Advanced Materials 25 (45): 6594–6601. doi:10.1002/adma.201302453. PMID 24166972. Bibcode: 2013AdM....25.6594Y.
- ↑ Yang, Y.; Zhang, H.; Chen, J.; Jing, Q.; Zhou, Y. S.; Wen, X.; Wang, Z. L. (2013). "Single-Electrode-Based Sliding Triboelectric Nanogenerator for Self-Powered Displacement Vector Sensor System". ACS Nano 7 (8): 7342–7351. doi:10.1021/nn403021m. PMID 23883397.
- ↑ Yang, W.; Chen, J.; Zhu, G.; Wen, X.; Bai, P.; Su, Y.; Lin, Y.; Wang, Z. (2013). "Harvesting vibration energy by a triple-cantilever based triboelectric nanogenerator". Nano Research 6 (12): 880–886. doi:10.1007/s12274-013-0364-0.
- ↑ Yang, W.; Chen, J.; Zhu, G.; Yang, J.; Bai, P.; Su, Y.; Jing, Q.; Cao, X. et al. (2013). "Harvesting Energy from the Natural Vibration of Human Walking". ACS Nano 7 (12): 11317–11324. doi:10.1021/nn405175z. PMID 24180642.
- ↑ Chen, J.; Zhu, G.; Yang, W.; Jing, Q.; Bai, P.; Yang, Y.; Hou, T. C.; Wang, Z. L. (2013). "Harmonic-Resonator-Based Triboelectric Nanogenerator as a Sustainable Power Source and a Self-Powered Active Vibration Sensor". Advanced Materials 25 (42): 6094–6099. doi:10.1002/adma.201302397. PMID 23999798. Bibcode: 2013AdM....25.6094C.
- ↑ Xie, Yannan; Wang, Sihong; Lin, Long; Jing, Qingshen; Lin, Zong-Hong; Niu, Simiao; Wu, Zhengyun; Wang, Zhong Lin (2013-06-14). "Rotary Triboelectric Nanogenerator Based on a Hybridized Mechanism for Harvesting Wind Energy". ACS Nano 7 (8): 7119–7125. doi:10.1021/nn402477h. ISSN 1936-0851. PMID 23768179. http://dx.doi.org/10.1021/nn402477h.
- ↑ Hu, Youfan; Yang, Jin; Jing, Qingshen; Niu, Simiao; Wu, Wenzhuo; Wang, Zhong Lin (2013-10-31). "Triboelectric Nanogenerator Built on Suspended 3D Spiral Structure as Vibration and Positioning Sensor and Wave Energy Harvester". ACS Nano 7 (11): 10424–10432. doi:10.1021/nn405209u. ISSN 1936-0851. PMID 24168315. http://dx.doi.org/10.1021/nn405209u.
- ↑ Yang, Ya; Zhang, Hulin; Liu, Ruoyu; Wen, Xiaonan; Hou, Te-Chien; Wang, Zhong Lin (2013-07-16). "Fully Enclosed Triboelectric Nanogenerators for Applications in Water and Harsh Environments". Advanced Energy Materials 3 (12): 1563–1568. doi:10.1002/aenm.201300376. ISSN 1614-6832. http://dx.doi.org/10.1002/aenm.201300376.
- ↑ Xie, Yannan; Wang, Sihong; Niu, Simiao; Lin, Long; Jing, Qingshen; Su, Yuanjie; Wu, Zhengyun; Wang, Zhong Lin (May 2014). "Multi-layered disk triboelectric nanogenerator for harvesting hydropower". Nano Energy 6: 129–136. doi:10.1016/j.nanoen.2014.03.015. ISSN 2211-2855. http://dx.doi.org/10.1016/j.nanoen.2014.03.015.
- ↑ Super-Durable and Highly Efficient Electrostatic Induced Nanogenerator Circulation Network Initially Charged by a Triboelectric Nanogenerator for Harvesting Environmental Energy. doi:10.1021/acsnano.0c10840.s002. http://dx.doi.org/10.1021/acsnano.0c10840.s002. Retrieved 2021-11-19.
- ↑ All-Weather Droplet-Based Triboelectric Nanogenerator for Wave Energy Harvesting. doi:10.1021/acsnano.1c02790.s002. http://dx.doi.org/10.1021/acsnano.1c02790.s002. Retrieved 2021-11-19.
- ↑ Carbon Dot-Based Composite Films for Simultaneously Harvesting Raindrop Energy and Boosting Solar Energy Conversion Efficiency in Hybrid Cells. doi:10.1021/acsnano.0c03986.s001. http://dx.doi.org/10.1021/acsnano.0c03986.s001. Retrieved 2021-11-19.
- ↑ Sala de Medeiros, Marina; Chanci, Daniela; Moreno, Carolina; Goswami, Debkalpa; Martinez, Ramses V. (2019-07-25). "Waterproof, Breathable, and Antibacterial Self-Powered e-Textiles Based on Omniphobic Triboelectric Nanogenerators" (in en). Advanced Functional Materials 29 (42): 1904350. doi:10.1002/adfm.201904350. ISSN 1616-301X.
- ↑ Fan, F. R.; Lin, L.; Zhu, G.; Wu, W.; Zhang, R.; Wang, Z. L. (2012). "Transparent Triboelectric Nanogenerators and Self-Powered Pressure Sensors Based on Micropatterned Plastic Films". Nano Letters 12 (6): 3109–3114. doi:10.1021/nl300988z. PMID 22577731. Bibcode: 2012NanoL..12.3109F.
- ↑ Taghavi, Majid; Mattoli, Virgilio; Sadeghi, Ali; Mazzolai, Barbara; Beccai, Lucia (2 May 2014). "A Novel Soft Metal-Polymer Composite for Multidirectional Pressure Energy Harvesting". Advanced Energy Materials 4 (12): 1400024. doi:10.1002/aenm.201400024.
- ↑ Lin, L.; Xie, Y.; Wang, S.; Wu, W.; Niu, S.; Wen, X.; Wang, Z. L. (2013). "Triboelectric Active Sensor Array for Self-Powered Static and Dynamic Pressure Detection and Tactile Imaging". ACS Nano 7 (9): 8266–8274. doi:10.1021/nn4037514. PMID 23957827.
- ↑ Taghavi, Majid; Sedeghi, Ali; Mondini, Alessio; Mazzolai, Barbara; Beccai, Lucia; Mattoli, Virgilio (2015). "Triboelectric smart machine elements and self-powered encoder". Nano Energy 13: 92–102. doi:10.1016/j.nanoen.2015.02.011.
- ↑ Lin, Z. H.; Zhu, G.; Zhou, Y. S.; Yang, Y.; Bai, P.; Chen, J.; Wang, Z. L. (2013). "A Self-Powered Triboelectric Nanosensor for Mercury Ion Detection". Angewandte Chemie 125 (19): 5169–5173. doi:10.1002/ange.201300437. PMID 23568745. Bibcode: 2013AngCh.125.5169L.
- ↑ Zi, Yunlong; Niu, Simiao; Wang, Jie; Wen, Zhen; Tang, Wei; Wang, Zhong Lin (2015). "Standards and Figure-of-Merits for Quantifying the Performance of Triboelectric Nanogenerators". Nature Communications 6:8376: 8376. doi:10.1038/ncomms9376. PMID 26406279. Bibcode: 2015NatCo...6.8376Z.
- ↑ Jump up to: 60.0 60.1 Xia, Xin; Fu, Jingjing; Zi, Yunlong (2019). "A Universal Standardized Method for Output Capability Assessment of Nanogenerators". Nature Communications 10:4428 (1): 4428. doi:10.1038/s41467-019-12465-2. PMID 31562336. Bibcode: 2019NatCo..10.4428X.
- ↑ Zi, Yunlong; Wu, Changsheng; Ding, Wenbo; Wang, Zhong Lin (2017). "Maximized Effective Energy Output of Contact-Separation-Triggered Triboelectric Nanogenerators as Limited by Air Breakdown". Advanced Functional Materials 27 (24): 1700049. doi:10.1002/adfm.201700049.
- ↑ Xu, Guoqiang; Li, Xiaoyi; Xia, Xin; Fu, Jingjing; Ding, Wenbo; Zi, Yunlong (2019). "On the force and energy conversion in triboelectric nanogenerators". Nano Energy 59: 154–161. doi:10.1016/j.nanoen.2019.02.035.
- ↑ Niu, Simiao; Wang, Zhong Lin (2015). "Theoretical systems of triboelectric nanogenerators". Nano Energy 14: 161–191. doi:10.1016/j.nanoen.2014.11.034.
- ↑ Liu, Di; Yin, Xing; Guo, Hengyu; Zhou, Linglin; Li, Xinyuan; Zhang, Chunlei; Wang, Jie; Wang, Zhong Lin (2019). "A constant current triboelectric nanogenerator arising from electrostatic breakdown". Science Advances 5 (4): eaav6437. doi:10.1126/sciadv.aav6437. PMID 30972365. Bibcode: 2019SciA....5.6437L.
- ↑ Zhao, Zhihao; Dai, Yejing; Liu, Di; Zhou, Linglin; Li, Shaoxin; Wang, Zhong Lin; Wang, Jie (2020-12-03). "Rationally patterned electrode of direct-current triboelectric nanogenerators for ultrahigh effective surface charge density" (in en). Nature Communications 11 (1): 6186. doi:10.1038/s41467-020-20045-y. ISSN 2041-1723. PMID 33273477. Bibcode: 2020NatCo..11.6186Z.
- ↑ Yang, Y.; Pradel, K. C.; Jing, Q.; Wu, J. M.; Zhang, F.; Zhou, Y.; Zhang, Y.; Wang, Z. L. (2012). "Thermoelectric Nanogenerators Based on Single Sb-Doped ZnO Micro/Nanobelts". ACS Nano 6 (8): 6984–6989. doi:10.1021/nn302481p. PMID 22742540.
- ↑ Zook, J. D.; Liu, S. T. (1978). "Pyroelectric effects in thin film". Journal of Applied Physics 49 (8): 4604. doi:10.1063/1.325442. Bibcode: 1978JAP....49.4604Z.
- ↑ Yang, Y.; Guo, W.; Pradel, K. C.; Zhu, G.; Zhou, Y.; Zhang, Y.; Hu, Y.; Lin, L. et al. (2012). "Pyroelectric Nanogenerators for Harvesting Thermoelectric Energy". Nano Letters 12 (6): 2833–2838. doi:10.1021/nl3003039. PMID 22545631. Bibcode: 2012NanoL..12.2833Y.
- ↑ Ye, C. P.; Tamagawa, T.; Polla, D. L. (1991). "Experimental studies on primary and secondary pyroelectric effects in Pb(ZrOxTi1−x)O3, PbTiO3, and ZnO thin films". Journal of Applied Physics 70 (10): 5538. doi:10.1063/1.350212. Bibcode: 1991JAP....70.5538Y.
- ↑ Yang, Y.; Jung, J. H.; Yun, B. K.; Zhang, F.; Pradel, K. C.; Guo, W.; Wang, Z. L. (2012). "Flexible Pyroelectric Nanogenerators using a Composite Structure of Lead-Free KNbO3 Nanowires". Advanced Materials 24 (39): 5357–5362. doi:10.1002/adma.201201414. PMID 22837044. Bibcode: 2012AdM....24.5357Y.
- ↑ Yang, Y.; Zhou, Y.; Wu, J. M.; Wang, Z. L. (2012). "Single Micro/Nanowire Pyroelectric Nanogenerators as Self-Powered Temperature Sensors". ACS Nano 6 (9): 8456–8461. doi:10.1021/nn303414u. PMID 22900676.
External links
- Professor Z. L. Wang's Nano Research Group at Georgia Institute of Technology
- Nano Electronic Science & Engineering Laboratory (NESEL) at Sungkyunkwan University (SKKU)
- Laboratory for Nanoscale Mechanics and Physics at University of Illinois, Urbana-Champaign
- LINLAB at University of California, Berkeley
- Samsung Advanced Institute of Technology
![]() | Original source: https://en.wikipedia.org/wiki/Nanogenerator.
Read more |