Organization:Fume hood
![]() A common modern fume hood. | |
Other names |
|
---|---|
Uses | Fume removal; Blast or flame shield |
Related items | Laminar flow cabinet Biosafety cabinet |
A fume hood (sometimes called a fume cupboard or fume closet) is a type of local ventilation device that is designed to limit exposure to hazardous or toxic fumes, vapors or dusts. The device is an enclosure with a movable sash window on one side that traps and exhausts gases and particulates either out of the area (through a duct) or back into the room (through air filtration), and is most frequently used in laboratory settings.
The first fume hoods, constructed from wood and glass, were developed in the early 1900s as a measure to protect individuals from harmful gaseous reaction by-products. Later developments in the 1970s and 80s allowed for the construction of more efficient devices out of epoxy powder-coated steel and flame-retardant plastic laminates.
Description
File:Fume hood - dry ice fog.webm A fume hood is typically a large piece of equipment enclosing five sides of a work area, the bottom of which is most commonly located at a standing work height (at least 28 to 34 inches (71 to 86 cm) above the floor).[1](p20) Fume hoods are most often found in laboratories that require the use of materials that may produce harmful particulates, gaseous by-products, or aerosols of hazardous materials such as those found in biocontainment laboratories.[1]
Two main types of fume hood exist: ducted and recirculating (ductless). The principle is the same for both types: air is drawn in from the front (open) side of the cabinet, and either expelled outside the building or made safe through filtration and fed back into the room.[2] This method of airflow control is intended to:
- protect the user from inhaling toxic gases (fume hoods, biosafety cabinets, glove boxes)
- protect the product or experiment (biosafety cabinets, glove boxes)
- protect the environment (recirculating fume hoods, certain biosafety cabinets, and any other type when fitted with appropriate filters in the exhaust airstream)
Secondary functions of these devices may include explosion protection, spill containment, and other functions necessary to the work being done within the device; these functions may be achieved through optimal placement of the fume hood in a room.[3]:{{{1}}}
Fume hoods are generally set back against the walls and are often fitted with infills above, to cover up the exhaust ductwork. Because of their recessed shape they are generally poorly illuminated by general room lighting, so many have internal lights with vapor-proof covers.[4] The front of the device includes a sash window, usually in glass or otherwise transparent glazing, which is able to slide vertically or horizontally.[3] Specialty enclosures for teaching may allow for additional visibility by constructing the sides and back of the unit from tempered glass, intended so that several individuals can look into a fume hood at once.[1](p9) Some models built for educational purposes ("student workstations") are portable and can be transported between locations or are built on a movable island;[5] they are often built with less demanding restrictions on chemical resistance.[6]
Fume hoods are generally available in 5 different widths; 1000 mm, 1200 mm, 1500 mm, 1800 mm and 2000 mm.[7] The depth varies between 700 mm and 900 mm, and the height between 1900 mm and 2700 mm. These designs can accommodate from one to three operators. All modern designs are required to be fitted with air flow meters to ensure that the hood is working properly while in use.
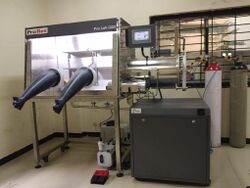
For exceptionally hazardous materials, an enclosed glovebox may be used, which completely isolates the operator from all direct physical contact with the work material and tools.[1]
Build materials
Several common materials used for the exterior construction of a modern fume hood include:[1]
- Mild steel, powder coated: The traditional method of building fume cupboards is from a zinc coated mild steel. Low cost, but has corrosion issues over time and a high carbon footprint to manufacture.
- Stainless steel: Typically used in radioactive applications, in cleanrooms, or in ATEX environments.
- Polypropylene: A modern build material with a greater chemical resistance than some contemporary materials. Lower environmental impact to produce than mild steel or stainless steel, but less heat resistant.
Liner materials
The interior of a fume hood is often subject to damaging chemicals and elevated temperatures, and as such it is often lined with materials resistant to the chemicals and environment it is expected to be subject to:[1]
- Phenolic resin for general applications;
- Fiber-reinforced plastic;
- Epoxy resin;
- Polypropylene;
- Square-corner stainless steel for durability and heat resistance;
- Coved-corner stainless steel is easier to decontaminate, for radiochemical and biohazard applications; and
- Cement board for rough usage.
Control and monitoring panels
Most fume hoods are fitted with a mains-powered control panel and/or air flow-monitoring device. Typically, they will allow for the manual or automatic adjustment of internal baffles, but are required by ANSI standards to warn of the following situations:[8](p7)
- Air flow is too high or low
- Too large an opening at the front of the unit (a "high sash" alarm is caused by the sliding glass at the front of the unit being raised higher than is considered safe, due to the resulting air velocity drop)
Some control panels additionally allow for switching mechanisms inside the hood from a central point, such as turning the exhaust fan or an internal light on or off.[4]
Ducted fume hoods
Most fume hoods for industrial purposes are ducted. A large variety of ducted fume hoods exist. In most designs, conditioned (i.e. heated or cooled) air is drawn from the lab space into the fume hood and then dispersed via ducts into the outside atmosphere.
The fume hood is only one part of the lab ventilation system. Because recirculation of lab air to the rest of the facility is not permitted, air handling units serving the non-laboratory areas are kept segregated from the laboratory units. To improve indoor air quality, some laboratories also utilize single-pass air handling systems, wherein air that is heated or cooled is used only once prior to discharge. Many laboratories continue to use return air systems to the laboratory areas to minimize energy and running costs, while still providing adequate ventilation rates for acceptable working conditions. The fume hoods serve to evacuate hazardous levels of contaminant.
To reduce lab ventilation energy costs, variable air volume (VAV) systems are employed, which reduce the volume of the air exhausted as the fume hood sash is closed. This product is often enhanced by an automatic sash closing device, which will close the fume hood sash when the user leaves the fume hood face. The result is that the hoods are operating at the minimum exhaust volume whenever no one is actually working in front of them.
Since the typical fume hood in US climates uses 3.5 times as much energy as a home,[9] the reduction or minimization of exhaust volume is strategic in reducing facility energy costs as well as minimizing the impact on the facility infrastructure and the environment. Particular attention must be paid to the exhaust discharge location, to reduce risks to public safety, and to avoid drawing exhaust air back into the building air supply system.
Auxiliary air
This method is outdated technology. The premise was to bring non-conditioned outside air directly in front of the hood so that this was the air exhausted to the outside. This method does not work well when the climate changes as it pours frigid or hot and humid air over the user making it very uncomfortable to work or affecting the procedure inside the hood. This system also uses additional ductwork which can be costly.
Constant air volume (CAV)
In a survey of 247 lab professionals conducted in 2010, Lab Manager Magazine found that approximately 43% of fume hoods are conventional CAV fume hoods.[10]
Non-bypass CAV
Closing the sash on a non-bypass CAV hood will increase face velocity (inflow velocity or "pull"),[lower-alpha 1] which is a function of the total volume divided by the area of the sash opening. Thus, a conventional hood's performance (from a safety perspective) depends primarily on sash position, with safety increasing as the hood is drawn closed.[12] To address this issue, many conventional CAV hoods specify a maximum height that the fume hood can be open in order to maintain safe airflow levels.
A major drawback of conventional CAV hoods is that when the sash is closed, velocities can increase to the point where they disturb instrumentation and delicate apparatuses, cool hot plates, slow reactions, and/or create turbulence that can force contaminants into the room.[13]
Bypass CAV
Bypass CAV hoods (which are sometimes also referred to as conventional hoods) were developed to overcome the high velocity issues that affect conventional fume hoods. These hood allows air to be pulled through a "bypass" opening from above as the sash closes. The bypass is located so that as the user closes the sash, the bypass opening gets larger. The air going through the hood maintains a constant volume no matter where the sash is positioned and without changing fan speeds. As a result, the energy consumed by CAV fume hoods (or rather, the energy consumed by the building HVAC system and the energy consumed by the hood's exhaust fan) remains constant, or near constant, regardless of sash position.[14]
Low flow/high performance bypass CAV
"High-performance" or "low-flow" bypass CAV hoods are the newest type of bypass CAV hoods and typically display improved containment, safety, and energy conservation features. Low-flow/high performance CAV hoods generally have one or more of the following features: sash stops or horizontal-sliding sashes to limit the openings; sash position and airflow sensors that can control mechanical baffles; small fans to create an air-curtain barrier in the operator's breathing zone; refined aerodynamic designs and variable dual-baffle systems to maintain laminar (undisturbed, nonturbulent) flow through the hood. Although the initial cost of a high-performance hood is typically more than that of a conventional bypass hood, the improved containment and flow characteristics allow these hoods to operate at a face velocity as low as 60 fpm, which can translate into $2,000 per year or more in energy savings, depending on hood size and sash settings.[15]
Reduced air volume (RAV)
Reduced air volume hoods (a variation of low-flow/high performance hoods) incorporate a bypass block to partially close off the bypass, reducing the air volume and thus conserving energy. Usually, the block is combined with a sash stop to limit the height of the sash opening, ensuring a safe face velocity during normal operation while lowering the hood's air volume. By reducing the air volume, the RAV hood can operate with a smaller blower, which is another cost-saving advantage.
Since RAV hoods have restricted sash movement and reduced air volume, these hoods are less flexible in what they can be used for and can only be used for certain tasks. Another drawback to RAV hoods is that users can in theory override or disengage the sash stop. If this occurs, the face velocity could drop to an unsafe level. To counter this condition, operators must be trained never to override the sash stop while in use, and only to do so when loading or cleaning the hood.[16]
Variable air volume (VAV)
VAV hoods, the newest generations of laboratory fume hoods, vary the volume of room air exhausted while maintaining the face velocity at a set level. Different VAV hoods change the exhaust volume using different methods, such as a damper or valve in the exhaust duct that opens and closes based on sash position, or a blower that changes speed to meet air-volume demands. Most VAV hoods integrate a modified bypass-block system that ensures adequate airflow at all sash positions. VAV hoods are connected electronically to the laboratory building's HVAC, so hood exhaust and room supply are balanced. In addition, VAV hoods feature monitors and/or alarms that warn the operator of unsafe hood-airflow conditions.
Although VAV hoods are much more complex than traditional constant-volume hoods, and correspondingly have higher initial costs, they can provide considerable energy savings by reducing the total volume of conditioned air exhausted from the laboratory. Since most hoods are operated the entire time a laboratory is open, this can quickly add up to significant cost savings. These savings are, however, completely contingent on user behavior: the less the hoods are open (both in terms of height and in terms of time), the greater the energy savings. For example, if the laboratory's ventilation system uses 100% once-through outside air and the value of conditioned air is assumed to be $7 per CFM per year (this value would increase with very hot, cold or humid climates), a 6-foot VAV fume hood at full open for experiment set up 10% of the time (2.4 hours per day), at 18 inch working opening 25% of the time (6 hours per day), and completely closed 65% of the time (15.6 hours per day) would save approximately $6,000 every year compared to a hood that is fully open 100% of the time.[17][18]
Potential behavioral savings from VAV fume hoods are highest when fume hood density (number of fume hoods per square foot of lab space) is high. This is because fume hoods contribute to the achievement of lab spaces' required air exchange rates. Put another way, savings from closing fume hoods can only be achieved when fume hood exhaust rates are greater than the air exchange rate needed to achieve the required ventilation rate in the lab room. For example, in a lab room with a required air exchange rate of 2000 cubic feet per minute (CFM), if that room has just one fume hood which vents air at a rate of 1000 square feet per minute, then closing the sash on the fume hood will simply cause the lab room's air handler to increase from 1000 CFM to 2000 CFM, thus resulting in no net reduction in air exhaust rates, and thus no net reduction in energy consumption.[19]
In a survey of 247 lab professionals conducted in 2010, Lab Manager Magazine found that approximately 12% of fume hoods are VAV fume hoods.[20]
Canopy fume hoods
Canopy fume hoods, also called exhaust canopies, are similar to the range hoods found over stoves in commercial and some residential kitchens. They have only a canopy (and no enclosure and no sash) and are designed for venting non-toxic materials such as non-toxic smoke, steam, heat, and odors. In a survey of 247 lab professionals conducted in 2010, Lab Manager Magazine found that approximately 13% of fume hoods are ducted canopy fume hoods.[21]
Pros | Cons |
---|---|
Fumes are completely removed from the workplace. | Additional ductwork. |
Low maintenance. | Temperature controlled air is removed from the workplace. |
Quiet operation, due to the extract fan being some distance from the operator. | Fumes are often dispersed into the atmosphere, rather than being treated. |
Ductless (recirculating) fume hoods
These units generally have a fan mounted on the top (soffit) of the hood, or beneath the worktop. Air is sucked through the front opening of the hood and through a filter, before passing through the fan and being fed back into the workplace. With a ductless fume hood it is essential that the filter medium be able to remove the particular hazardous or noxious material being used. As different filters are required for different materials, recirculating fume hoods should only be used when the specific hazards are known and suited to the type of filter used. The production of recirculating fume hoods was only made possible after the invention of the HEPA filter in the 1940s.[22]
Ductless Hoods with the fan mounted below the work surface are not recommended as the majority of vapours rise and therefore the fan will have to work a lot harder (which may result in an increase in noise) to pull them downwards. Units with the fan mounted above the work surface have been proven to offer greater levels of safety.
Air filtration of ductless fume hoods is typically broken into two segments:
- Pre-filtration: This is the first stage of filtration, and consists of a physical barrier, typically open cell foam, which prevents large particles from passing through. Filters of this type are generally inexpensive, and last for approximately six months depending on usage.
- Main filtration: After pre-filtration, the fumes are sucked through a layer of activated charcoal which absorbs the majority of chemicals that pass through it. Ammonia and carbon monoxide will, however, pass through most carbon filters. Additional specific filtration techniques can be added to combat chemicals that would otherwise be pumped back into the room. A main filter will generally last for approximately two years, dependent on usage.
Ductless fume hoods are sometimes not appropriate for research applications where the activity, and the materials used or generated, may change or be unknown. As a result of this and other drawbacks, some research organizations, including the University of Wisconsin, Milwaukee,[23] Columbia University,[24] Princeton University,[25] the University of New Hampshire,[26] and the University of Colorado, Boulder[27] either discourage or prohibit the use of ductless fume hoods.
A benefit of ductless fume hoods is that they are mobile, easy to install since they require no ductwork, and can be plugged into a 120 volt or 240 volt outlet.
In a survey of 247 lab professionals conducted in 2010, Lab Manager Magazine found that approximately 22% of fume hoods are ductless fume hoods.[28]
Pros | Cons |
---|---|
Ductwork not required. | Filters must be regularly maintained and replaced. |
Temperature controlled air is not removed from the workplace. | Greater risk of chemical exposure than with ducted equivalents. |
Contaminated air is not pumped into the atmosphere. | The extract fan is near the operator, so noise may be an issue. |
Specialty designs
Acid digestion
These units are typically constructed of polypropylene to resist the corrosive effects of acids at high concentrations. If hydrofluoric acid is being used in the hood, the hood's transparent sash should be constructed of polycarbonate which resists etching better than glass. Hood ductwork should be lined with polypropylene or coated with PTFE (Teflon).
Downflow
Downflow fume hoods, also called downflow work stations, are typically ductless fume hoods designed to protect the user and the environment from hazardous vapors generated on the work surface. A downward air flow is generated and hazardous vapors are collected through slits in the work surface.
Perchloric acid
These units feature a waterwash system (not to be confused with a scrubber - see below) in the ductwork. Because dense perchloric acid fumes settle and form explosive crystals, it is vital that the internal baffles of the fume cupboard and ductwork be cleaned internally with a series of sprayers.
Radioisotope
This fume hood is made with a coved stainless steel liner and coved integral stainless steel countertop that is reinforced to handle the weight of lead bricks or blocks.
Scrubber
This type of fume hood absorbs the fumes through a chamber filled with plastic shapes (Pall Rings), which are doused with a scrubbing medium. The chemicals are washed into a sump, which is often filled with a neutralizing liquid such as caustic soda. The fumes are then dispersed, or disposed of, in the conventional manner.
Waterwash
These fume hoods have an internal wash system that cleans the interior of the unit, to prevent a build-up of dangerous chemicals.
Floor-mounted
Also termed "walk-in" fume hoods, floor-mounted fume hoods have a working area that extends from the floor to the bottom of a connected exhaust duct for the use of tall equipment. Despite the name of "walk-in", entering a floor-mounted fume hood in operation while it contains hazardous materials poses a significant risk to the user.[29]
Energy consumption
Because fume hoods constantly remove very large volumes of conditioned (heated or cooled) air from lab spaces, they are responsible for the consumption of large amounts of energy. Energy costs for a typical hood range from $4,600/year for moderate climates such as Los Angeles , to $9,300/year for extreme cooling climates such as Singapore.[30] Fume hoods are a major factor in making laboratories four to five times more energy intensive than typical commercial buildings.[31] The bulk of the energy that fume hoods are responsible for is the energy needed to heat and/or cool air delivered to the lab space. Additional electricity is consumed by fans in the HVAC system and fans in the fume hood exhaust system.[32]
A number of universities run or have run programs to encourage lab users to reduce fume hood energy consumption by keeping VAV sashes closed as much as possible. For example, Harvard University's Chemistry & Chemical Biology Department ran a "Shut the sash" campaign, which resulted in a sustained ~30% reduction in fume hood exhaust rates. This translated into cost savings of approximately $180,000 per year, and a reduction in annual greenhouse gas emissions equivalent to 300 metric tons of carbon dioxide.[33] Other institutions reporting programs to reduce energy consumption by fume hoods include Massachusetts Institute of Technology,[34] North Carolina State University,[35] University of British Columbia,[36][37] University of California, Berkeley,[38] University of California, Davis,[39] University of California, Irvine,[40] University of California, Los Angeles,[41][42][43] University of California, Riverside,[44] University of California, San Diego,[45] University of California, Santa Barbara,[46] University of Central Florida[47] and University of Colorado, Boulder.[48]
Person detection technology can sense the presence of a hood operator within a zone in front of a hood. Zone presence sensor signals allow ventilation valve controls to switch between normal and stand by modes.[49] Coupled with laboratory space occupancy sensors these technologies can adjust ventilation to a dynamic performance objective.
Maintenance
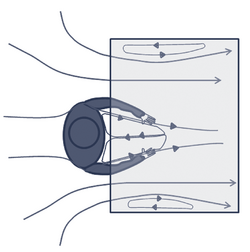
Fume hoods require regular maintenance to ensure consistent functionality; this is in addition to the standard precautions and measures taken during regular operations and ideally involves daily, periodic, and annual inspections:[50]
- Daily fume hood inspections entail visual inspections of the fume hood for improper storage of material and other visible blockages. Airflow is often monitored for these daily inspections by taping a piece of tissue paper to the open face of the hood such that it will be drawn inwards; if the tissue is not pulled inwards, the hood exhaust is not functioning.[51]
- Periodic fume hood function inspections require the measurement of capture or face velocity[lower-alpha 1] with an anemometer. Specialized instruments for measuring wind speed in a fume hood or in ductwork are often referred to by trade names, such as "velometer" and "vaneometer".[52] Hoods for most common chemicals have a minimum average face velocity of 100 feet (30 m) per minute at sash opening of 18 inches (460 mm). Face velocity readings should not vary by more than 20%. The minimum number of readings used to determine average face velocity varies according to ASHRAE standards, the most recent of which was produced in 2016.[53] Other local exhaust devices are smoke tested to determine if the contaminants they are designed to remove are being adequately captured by the hood.
- Annual maintenance involves mechanical repairs (i.e. lubrication, belt tension, fan blade deterioration) and maintenance as recommended by the device manufacturer, or to bring the device into compliance with standards if periodic inspections indicate sub-optimal performance. In some cases, large-scale upgrades may be required to maintain compliance, especially in older units as new occupational safety regulations come into effect,[54] such as those mandated in National Institutes of Health laboratories.[55]
History
The need for ventilation has been apparent from early days of chemical research and education. Some early approaches to the problem were adaptations of the conventional chimney.[56] A hearth constructed by Thomas Jefferson in 1822–1826 at the University of Virginia was equipped with a sand bath and special flues to vent toxic gases.[57]
In 1904 the newly built Chemical Faculty at the Technical University in Gdańsk was equipped with fume hoods made of wood and glass in auditoria, several lecture rooms, student laboratories and rooms for scientists. Sliding up and down front panel with glass protected from fumes and explosions. Each fume hood was illuminated, equipped with gas installation for heating and running water with a drain. Harmful and corrosive gaseous byproducts of reactions were actively removed using the natural draft of a fireplace chimney. This early design is still functioning after over 110 years.[58]
The draft of a chimney was also used by Thomas Edison as what has been called the "first fume hood".[59] The first known modern "fume cupboard" design with rising sashes was introduced at the University of Leeds in 1923.[22] 13 years later, Labconco, now a prominent fume hood manufacturer, developed the first fume hood for commercial sale, reminiscent of modern designs with a front-facing sash window.[22]
Modern fume hoods are distinguished by methods of regulating air flow independently of combustion, improving efficiency and potentially removing volatile chemicals from exposure to flame. Fume hoods were originally manufactured from wood, but during the 1970s and 1980s epoxy powder-coated steel became the norm. During the 1990s, wood pulp derivatives treated with phenolic resin (plastic laminates and solid grade laminates) for chemical resistance and flame spread retardance started to become widely accepted.
See also
Notes
References
- ↑ 1.0 1.1 1.2 1.3 1.4 1.5 ((Labconco)) (2003). "How To Select The Right Laboratory Hood System". https://research.unl.edu/docs/VentilationSelectFumeHood_2-07.pdf.
- ↑ Peat, Kay (August 16, 2022). "For Your Lab: Ducted or Ductless Fume Hoods?". https://www.triumvirate.com/blog/for-your-lab-ducted-or-ductless-fume-hoods.
- ↑ 3.0 3.1 ((University of Toronto Environmental Health and Safety)) (November 2018). "Design Standard - Fume Hoods & Fume Hood Exhausts". https://ehs.utoronto.ca/wp-content/uploads/2018/12/Fume-Hoods-03-Design-Standard_November-2018.pdf.
- ↑ 4.0 4.1 "3.11 Fume Hood Power and Electrical". https://ehs.stanford.edu/manual/laboratory-standard-design-guidelines/fume-hood-power-and-electrical.
- ↑ "CLEAR VIEW FUME HOODS". https://www.belart.com/clear-view-fume-hoods.html.
- ↑ "Fume Hoods Overview". 2015. https://www.newenglandlab.com/userfiles/files/resources/Catalog%20Sections/Mott%209_1/9_1-P-FUME-HOODS-NEL.pdf.
- ↑ Pickard, Quentin (2002). "Laboratories". The Architects' Handbook. Oxford, England: Wiley-Blackwell. p. 228. ISBN 1-4051-3505-0.
- ↑ "Laboratory Guidelines and Standards Application Note LC-125 Rev C (US)". January 6, 2023. https://tsi.com/getmedia/ed63b48a-7f5a-4981-911e-7f33694809bc/LC-125_Lab-Guidelines-and-Standards_RevC_US.
- ↑ Mills, Evan; Dale Sartor (April 2006). "Energy Use and Savings Potential for Laboratory Fume Hoods". LBNL 55400. http://evanmills.lbl.gov/pubs/pdf/fh_energy_full_report.pdf. Retrieved 23 October 2012.
- ↑ "Shopping for a Fume Hood? See the Survey Results". Lab Manager Magazine. Jan 1, 2011. http://www.labmanager.com/?articles.view/articleNo/3857/article/Shopping-for-a-Fume-Hood--See-the-Survey-Results.
- ↑ Harris, Cyril M. (2005). "face velocity". face velocity (4th ed.). New York: McGraw-Hill. ISBN 9780071452373.
- ↑ McLeod, Vince; Glenn Ketcham (October 7, 2009). "CAV, RAV & VAV". Lab Manager Magazine. http://www.labmanager.com/?articles.view/articleNo/3463/.
- ↑ McLeod, Vince; Glenn Ketcham (October 7, 2009). "CAV, RAV & VAV". Lab Manager Magazine. http://www.labmanager.com/?articles.view/articleNo/3463/.
- ↑ "Lab Fume Hoods". University of Colorado at Boulder Facilities Management. http://www.colorado.edu/FacMan/about/conservation/FumeHoods.html.
- ↑ "Lab Fume Hoods". University of Colorado at Boulder Facilities Management. http://www.colorado.edu/FacMan/about/conservation/FumeHoods.html.
- ↑ "Lab Fume Hoods". University of Colorado at Boulder Facilities Management. http://www.colorado.edu/FacMan/about/conservation/FumeHoods.html.
- ↑ "Fume Hood Sash Stickers Increases Laboratory Safety and Efficiency at Minimal Cost: Success at two University of California Campuses". US Department of Energy. March 2012. http://www1.eere.energy.gov/femp/pdfs/sash_stickers_cs.pdf.
- ↑ Wesolowski, Daniel; Elsa Olivetti; Amanda Graham; Steve Lanou; Peter Cooper; Jim Doughty; Rich Wilk; Leon Glicksman (10 Feb 2010). "The use of feedback in lab energy conservation: fume hoods at MIT". International Journal of Sustainability in Higher Education 11 (3): 217–235. doi:10.1108/14676371011058523. http://web.mit.edu/~slanou/www/shared_documents/The%20use%20of%20feedback%20in%20lab%20energy%20conservation.pdf.
- ↑ "Fume Hood Sash Stickers Increases Laboratory Safety and Efficiency at Minimal Cost: Success at two University of California Campuses". US Department of Energy. March 2012. http://www1.eere.energy.gov/femp/pdfs/sash_stickers_cs.pdf.
- ↑ "Shopping for a Fume Hood? See the Survey Results". Lab Manager Magazine. Jan 1, 2011. http://www.labmanager.com/?articles.view/articleNo/3857/article/Shopping-for-a-Fume-Hood--See-the-Survey-Results.
- ↑ "Shopping for a Fume Hood? See the Survey Results". Lab Manager Magazine. Jan 1, 2011. http://www.labmanager.com/?articles.view/articleNo/3857/article/Shopping-for-a-Fume-Hood--See-the-Survey-Results.
- ↑ 22.0 22.1 22.2 John Buie (2011-12-09). "Evolution of Fume Hoods". Lab Manager. http://www.labmanager.com/lab-product/2011/12/evolution-of-fume-hoods?fw1pk=2#.Uqp6AI72iZZ.
- ↑ "UW Milwaukee Ductless Fume Hood Policy". http://www4.uwm.edu/usa/safety/laboratory_safety/ductless_fumehoods.cfm.
- ↑ "Columbia University Chemical Fume Hood Policy". http://ehs.columbia.edu/fhPolicy.html.
- ↑ "Princeton University Laboratory Safety Manual, Section 6B: Controlling Chemical Exposures". http://web.princeton.edu/sites/ehs/labsafetymanual/sec6b.htm.
- ↑ "University of New Hampshire Fume Hood Program". University of New Hampshire Office of Environmental Health and Safety. http://www.unh.edu/research/sites/unh.edu.research/files/docs/EHS/UNH-Fume-Hood-Program.pdf.
- ↑ "Fume Hood Questions & Answers". University of Colorado - Boulder Department of Environmental Health and Safety. http://www.colorado.edu/ehs/pdf/ECIH.FumeHoodQandA11_08.pdf.
- ↑ "Shopping for a Fume Hood? See the Survey Results". Lab Manager Magazine. Jan 1, 2011. http://www.labmanager.com/?articles.view/articleNo/3857/article/Shopping-for-a-Fume-Hood--See-the-Survey-Results.
- ↑ "Fume Hoods | Laboratory Safety". https://www.stpetersburg.usf.edu/safety-and-compliance/programs-and-services/laboratory-safety/fume-hoods.aspx.
- ↑ Mills, Evan; Dale Sartor (April 2006). "Energy Use and Savings Potential for Laboratory Fume Hoods". LBNL 55400. http://evanmills.lbl.gov/pubs/pdf/fh_energy_full_report.pdf. Retrieved 23 October 2012.
- ↑ Bell, G.; D. Sartor; E. Mills (October 2003). "The Berkeley Hood: Development and Commercialization of an Innovative High-Performance Laboratory Fume Hood: Progress Report and Research Status: 1995−2003". Lawrence Berkeley National Laboratory. http://ateam.lbl.gov/hightech/fumehood/doc/LBNL-48983_FY03.pdf.
- ↑ "Lab Fume Hoods". University of Colorado at Boulder Facilities Management. http://www.colorado.edu/FacMan/about/conservation/FumeHoods.html.
- ↑ Kreycik, Philip. "Energy - Shut the Sash Case Study". National Wildlife Federation - Campus Ecology. http://www.nwf.org/~/media/Campus-Ecology/Files/Case-Studies/Harvard-Shut-the-Sash-Final.ashx.
- ↑ Wesolowski, Daniel; Elsa Olivetti; Amanda Graham; Steve Lanou; Peter Cooper; Jim Doughty; Rich Wilk; Leon Glicksman (10 Feb 2010). "The use of feedback in lab energy conservation: fume hoods at MIT". International Journal of Sustainability in Higher Education 11 (3): 217–235. doi:10.1108/14676371011058523. http://web.mit.edu/~slanou/www/shared_documents/The%20use%20of%20feedback%20in%20lab%20energy%20conservation.pdf.
- ↑ "NC State: Shut the Sash". Sustainability at NC State. http://sustainability.ncsu.edu/campus/energy-water/education-awareness/shut-the-sash.
- ↑ "Shut the Sash". http://www.sustain.ubc.ca/campus-initiatives/green-research/shut-the-sash.
- ↑ "Shut the Sash Ends With a Bang". University of British Columbia Campus & Community Planning eNewsletter. May 2012. http://www.planning.ubc.ca/vancouver_home/news_and_events/enewsletter/may_2012/articles634.php.
- ↑ "Green Campus Projects". UC Berkeley Green Campus Chronicles. May 2011. http://tgif.berkeley.edu/docs/ucb_green_campus_chronicles_-_may_2011.pdf.
- ↑ "Fume Hood Sash Stickers Increases Laboratory Safety and Efficiency at Minimal Cost: Success at two University of California Campuses". US Department of Energy. March 2012. http://www1.eere.energy.gov/femp/pdfs/sash_stickers_cs.pdf.
- ↑ "UC-Irvine's "Shut the Sash" Campaign Counts Inches to Save Energy". National Wildlife Federation Blog. 2008-08-26. http://blog.nwf.org/2008/08/uc-irvines-shut-the-sash-campaign-counts-inches-to-save-energy/.
- ↑ "Behavioral Changes in Laboratory Energy Consumption – Fume Hoods". UCLA Laboratory Energy Efficiency Program. March 2009. http://ehs.ucla.edu/Pub/Fall08_FumeHoodResults.pdf.
- ↑ "We Want You To Shut Your Sash: UCLA Fume Hood Competition—Round Two!". http://ase.org/userfiles/13508_poster_official_final.pdf.
- ↑ "Fume Hood Competition". PowerSave Green Campus UCLA. http://powersavebruins.org/index.php/projects/fume-hood-competition.
- ↑ "Shut the Sash". UC Riverside Environmental Health & Safety. http://www.ehs.ucr.edu/safety/Fume_Hoods/shut_the_sash.html.
- ↑ University of California, San Diego 2012 STARS Submittal. University of California, San Diego. 2012. http://www.sierraclub.org/sierra/201209/coolschools/pdfs/university-of-california-san-diego-ca.pdf.
- ↑ "Fume Hood Sash Stickers Increases Laboratory Safety and Efficiency at Minimal Cost: Success at two University of California Campuses". US Department of Energy. March 2012. http://www1.eere.energy.gov/femp/pdfs/sash_stickers_cs.pdf.
- ↑ "Shut the Sash!". http://www.sustainable.ucf.edu/shut-sash.
- ↑ "Lab Fume Hoods". University of Colorado at Boulder Facilities Management. http://www.colorado.edu/FacMan/about/conservation/FumeHoods.html.
- ↑ Zone Presence Sensor [1] retrieved July, 2020
- ↑ "Fume Hood Maintenance". May 18, 2017. https://trimediaee.com/blog/industrial-hygiene/fume-hood-maintenance/.
- ↑ "Checking Fume Hoods". November 28, 2023. https://ysu.edu/eohs/cmc/sops/fumehoods.
- ↑ Matt (March 20, 2019). "Velometer". http://www.hvacspecialists.info/service/instruments-devices/velometer.html.
- ↑ ((Esco Lifesciences)) (27 January 2017). "Latest updates on ASHRAE Fume Hood Perfomance Testing Standard". https://www.escolifesciences.com/news/latest-updates-on-ashrae-fume-hood-perfomance-testing-standard.
- ↑ "Compliance, Safety & Energy Upgrades | Dynaflow" (in en-US). Dynaflow. https://dynaflow.com.au/products/compliance-safety-energy-upgrades/.
- ↑ "Fume Hood Requirements and Testing". July 2010. https://orf.od.nih.gov/TechnicalResources/Documents/News%20to%20Use%20PDF%20Files/2010%20NTU/July%20News%20to%20Use_508.pdf.
- ↑ George Wilson (1703). "A Compleat Course of Chymistry". Printed for Wm Turner at Lincolns-Inn Back Gate; and R. Baffet, at the Mitre in Fleetstreet. p. 158. https://books.google.com/books?id=zKVhAAAAcAAJ. "Sublimate of Corosive Arsnick: Let all your Operations be perform'd in a Chimney, that the Pernicious Fumes may be freely ascend without Prejudice to the Operator; and when you grind the Arsnick, Muffle your Mouth and Nostrils"
- ↑ Gillian Mohney (2015-10-18). "Thomas Jefferson's Hidden Chemistry Lab Discovered". ABC News. https://abcnews.go.com/Health/thomas-jeffersons-hidden-chemistry-lab-found-univ-virginia/story?id=34521301.
- ↑ Marzena Klimowicz-Sikorska (2010-09-30). "Wehikuł czasu na Politechnice Gdańskiej / Time machine at the Gdańsk University of Technology" (in pl). Trojmiasto.pl. http://www.trojmiasto.pl/wiadomosci/Wehikul-czasu-na-Politechnice-Gdanskiej-n42148.html.
- ↑ "Fume hood history". Labscape. http://www.labscape.com/fume-hood-history/.
External links
- Northwestern University Office for Research Safety - The Chemical Fume Hood Handbook
- Lab Manager Magazine: CAV, RAV & VAV
- University of Louisville's Chemical Hood User's Guide
- Information from the University of Bath in the UK
- The Fume Hood Resource Center by Lab Manager Magazine
- University of Toronto's Guide to running a sash-shutting campaign
- What is VAV and Why is It Important? - TION Article
![]() |
Wikimedia Commons has media related to Fume hood. |
![]() | Original source: https://en.wikipedia.org/wiki/Fume hood.
Read more |