Engineering:Cartridge (respirator)
}}
A respirator cartridge or canister is a container that cleans pollution from air. Employees working in a polluted atmosphere use respirators for health preservation. If the air in the workplace is polluted with noxious gases, but contains a lot of oxygen[1] they often use air-purifying respirators (APR). These respirators provide employees breathable air by removing pollution from ambient air using canisters or cartridges. There are cartridges of different types, and they must be chosen correctly and replaced in a timely manner[2].
Principles of purification of polluted air in APR
Absorption
Capture noxious gases may be accomplished by the sorbents.[3] These materials (activated carbon, aluminium oxide etc.) have a large specific surface area and can absorb gases. Typically, such sorbents used in the form of granules, and cartridge case is filled with them. Contaminated air travels through the bed of sorbent granules in the cartridge, and movable harmful gas molecules collide with the surface of the sorbent and remain therein. The sorbent has saturated the molecules caught and gradually loses its ability to capture the gases. So, contaminated air can pass through the saturated sorbent to the layers of fresh sorbent. The concentration of harmful substances in the purified air after prolonged use of the cartridge increases, and may exceed the Permissible Exposure Limit PEL. Therefore, the service life of the cartridges is limited. The bond strength between the captured molecule and sorbent has a small, and the molecule is able to separate from the sorbent and get into the air again. The ability of the sorbent to capture the gases depends on: the properties of the gases and their concentrations, the air temperature, the air relative humidity, the rate of air consumed by the employee, and many other factors. Activated carbon can be saturated with chemicals that make more stronger ties with molecules of trapped gases - to improve the capture of a number of harmful gases. The saturation of the activated carbon with iodine - improves the capture of mercury; saturation of metal salts - improves the capture of ammonia; saturation of metal oxides - improves capture acid gases.[4]
Chemical reaction between the gas and the absorber (chemisorption)
The ability of some harmful gases to react chemically with some other substances can be used to capture them. For example, the authors[3] describe the ability of copper salts to form complex compounds with ammonia. Creating strong links between the gas molecules and the sorbent may allow one the use of gas canisters repeatedly - if it has sufficient unsaturated sorbent.
Catalytic decomposition
Some harmful gases can be neutralized through catalytic oxidation. A hopcalite can oxidize toxic carbon monoxide, CO to harmless carbon dioxide. But the effectiveness of this catalyst strongly decreases with relative humidity increases. Therefore, there are some drier (desiccant) in the canisters (before such catalysts). A polluted air always contains water vapor, and after the saturation of the desiccant - catalyst ceases carbon monoxide neutralization.
Combined cartridges
If employer use combined (multigas) cartridges, that provide air purification from a combination of different harmful gases, they apply gas cartridges with such sorbents or/and catalysts, that is necessary to capture the gases; and such canister is subject to all relevant constraints.
Classification and marking of cartridges
United States
In the U.S., manufacturers can certify cartridges intended for purifying workplace air from various gaseous contaminants.[5]
Cartridges types in US | |
---|---|
Harmful substances | The color code[6]† |
Acid gases | White |
Acid gases and ammonia gas | Green with ½-inch white stripe completely around the canister near the bottom. |
Acid gases, ammonia, carbon monoxide and organic vapors | Red |
Acid gases and organic vapors | Yellow |
Acid gases, organic vapors and ammonia | Brown |
Ammonia gas | Green |
Ammonia and methylamine | Green |
Carbon monoxide | Blue |
Chemical, biological, radiological and nuclear substances (CBRN) | Black |
Chlorine gas | White with ½- inch yellow stripe completely around the canister near the bottom. |
Formaldehyde | Pale brown |
Hydrocyanic acid gas | White with ½-inch green strip completely around the canister near the bottom |
Organic vapors | Brown |
Other gases and vapors, not listed above | Olive color |
† Gray shall not be assigned as the main color for a canister designed to remove acids or vapors |
The orange color can be used for painting the entire cartridge housing, or as a strip. But this color is not in the table, and to determine from what protects the cartridge with such color one should read the inscription.
The legislation requires the employer to select cartridges using only labels and not the color of the markings (to reduce the risk of error).
European Union and RF
In the EU and in RF (Russian Federation),[7][8][9][10][11] manufacturers can certify cartridges intended for cleaning air of various gaseous contaminants. The codes are covered by EN14387, additionally particulate codes P1, P2 and P3 are used. For example, A1P2 is the code for commonly used filters in industry and agriculture that provide protection against A type gases and commonly occurring particulates.
Cartridges types in EU and RF | |||||
---|---|---|---|---|---|
Harmful substances | Marking | Color | Low sorbent capacity | Medium sorbent capacity | Large sorbent capacity |
Organic gases and vapors with boiling point above 65 °C recommended by the manufacturer | А | Brown | A1 | A2 | A3 |
Inorganic gases and vapors, with the exception of carbon monoxide, recommended by the manufacturer | В | Grey | В1 | В2 | В3 |
Sulphur dioxide and other acid gases and vapors recommended by the manufacturer | E | Yellow | Е1 | Е2 | Е3 |
Ammonia and its organic derivatives recommended by the manufacturer | K | Green | К1 | К2 | К3 |
Organic compounds with low boiling temperature (<65°С) recommended by the manufacturer | AX | Green | AX | ||
Particular gases specified by the manufacturer | SX | Violet | SX | ||
Nitric oxide NO (NO2) | NO | Blue and white | NO |
Cartridges AX, SX and NO not distinguish on the sorption capacity (as in the US) when they are classified and certified.
If the cartridge is designed to protect from several different types of harmful gases, in the designation contains the list of designations for specific types of perceived harmful gases, for example: A2B1, color - brown and grey.
Choice and timely replacement of cartridges
Selection of the cartridge should be carried out after determining the composition of the atmosphere in the workplace. To choose the right types of cartridges in the U.S., the employer may use the NIOSH guide[12] or the recommendations of the manufacturers. The service life of all types of cartridges is limited. Therefore, the employer is obliged to replace them in a timely manner.
Old methods
Use of subjective reactions of an employee’s sensory system
The use of cartridges in the contaminated atmosphere leads to saturation of the sorbent (or the dryer — when using catalysts). The concentration of harmful gases in the purified air gradually increases. The ingress of harmful gases in the inhaled air can lead to the reaction of the employee's sensory system: odor, taste, irritation of the respiratory system, dizziness, headaches, and other health impairments (up to loss of consciousness).[13]
These signs (known in the U.S. as "warning properties" - p. 28[13]) indicate that one must leave the polluted workplace area, and replace the cartridges with a new one. (This can also be a symptom of a loose fit the mask to one face and the leakage of unfiltered air through the gaps between the mask and the face). Historically, this method is the oldest.
The advantages of this method – if harmful gases have warning properties at concentrations less than 1 PEL, the replacement will be produced in a timely manner (in most cases, at least); the application of this method does not require the use of special cartridges (more expensive) and accessories; replacement happens when one needs to do it – after the sorbent saturation, and without any calculations; the sorption capacity of the cartridges is fully expired (which reduces costs for respiratory protection).
The disadvantage of this method is that some of harmful gases have no warning properties. For example, there is a list of more than 500 harmful gases in the[14] and more than 60 of them have no warning properties, and there are no any such information for more than one hundred of them. So, if one uses warning properties to replace cartridges, this leads to breathing air with excess harmful gas concentration in some cases. The table contains a list of the chemicals that have no warning properties.
Incomplete list of some harmful gases and vapors that have no warning properties | ||
---|---|---|
Gases and vapors (CAS) | PEL, ppm (mg/m3) | Concentration of odor threshold, PEL |
ethylene oxide (75-21-8) | 1 (1,8) | 851 |
arsine (7784-42-1) | 0,05 (0,2) | up to 200 |
pentaborane (19624-22-7) | 0,005 (0,013) | 194 |
Chlorine dioxide (10049-04-4) | 0,1 (0,3) | 92,4 |
Methylene diphenyl diisocyanate (101-68-8) | 0,005 (0,051) | 77 |
Diglycidyl ether (2238-07-5) | 0,1 (0,53) | 46 |
Vinylidene chloride (75-35-4) | 1 (4,33) | 35.5 |
Toluene-2,6-diisocyanate (91-08-7) | 0,005 (0,036) | 34 |
Diborane (19287-45-7) | 0,1 (0,1) | 18-35 |
Cyanogen (460-19-5) | 10 (21) | 23 |
Propylene oxide (75-56-9) | 2 (4,75) | 16 |
Methyl 2-cyanoacrylate (137-05-3) | 0,2 (1) | 10 |
Osmium tetroxide (20816-12-0) | 0,0002 (0,0016) | 10 |
Benzene (71-43-2) | 1 (3,5) | 8,5 |
Selenide (7783-07-5) | 0,05 (0,2) | 6 |
Formic acid (64-18-6) | 5 (9) | 5,6 |
Phosgene (75-44-5) | 0,1 (0,4) | 5,5 |
Methylcyclohexanol (25639-42-3) | 50 (234) | 5 |
P-tert-Butyltoluene (98-51-1) | 1 (6,1) | 5 |
Perchloryl fluoride (7616-94-6) | 3 (13) | 3,6 |
Maleic anhydride (108-31-6) | 0,1 (0,4) | 3,18 |
Hexachlorocyclopentadiene (77-47-4) | 0,01 (0,11) | 3 |
1,1-dichloroethane (75-34-3) | 100 (400) | 2,5 |
Bromochloromethane (74-97-5) | 200 (1050) | 2 |
N-Propyl nitrate (627-13-4) | 25 (107) | 2 |
Oxygen difluoride (7783-41-7) | 0,05 (0,1) | 1.9 |
Methylcyclohexane (108-87-2) | 400 (1610) | 1,4 |
Chloroform (67-66-3) | 10 (49) | 1,17 |
If the threshold odor of pentaborane is 194 PEL; and if its concentration is only 10 PEL, one cannot timely change cartridges with using smell - they could be "used" forever (but they cannot protect forever).
Practice has shown that the presence of warning properties not always leads to the timely replacement of cartridges.[15] A study[16] showed that on average 95% of a group of people has an individual threshold of olfactory sensitivity in the range of from 1/16 to 16 from the mean. This means that 2.5% of people will not be able to smell harmful gases at a concentration 16 times greater than the average threshold of perception of a smell. The threshold of sensitivity of different people can vary by two orders of magnitude. That is, 15% of people do not smell at concentrations 4 times higher sensitivity threshold. The value of threshold smell greatly depends on how much attention people pay this, and on their health status.
The sensitivity of people may be reduced, for example - when colds and other diseases. It turned out that worker's ability to detect the smell also depends on the nature of the work to be performed — if it requires concentration, an employee doesn't react to the smell. Prolonged exposure to harmful gases (for example, hydrogen sulfide) at low concentration can create a olfactory fatigue, which reduces sensitivity. In all of these cases employees can be exposed to harmful substances with the concentration larger than 1 PEL, and it may lead to the development of occupational diseases.
This was the reason for the ban to use this method of cartridges replacement in the U.S. since 1996 (the Occupational Safety and Health Administration OSHA standard).[13]
Increase in mass of the cartridges with desiccant
To protect workers from carbon monoxide often use cartridges with catalyst - hopcalite. This catalyst does not change its properties over time of use, but when it moistened, the degree of protection significantly reduced. Because water vapor is always present in the air, the polluted air is dehumidified in the cartridge (for use of the catalyst). Due to the fact that the mass of water vapor in the polluted air is much greater than the mass of harmful gases, trapping moisture from the air leads to a significantly higher increase in the mass of cartridges than the trapping gases. This is a substantial difference, and it can be used to determine whether to continue to use gas cartridges further without replacement. The cartridge was weighed, and a decision can be made based on the magnitude of increase of its mass. For example, the book[17] describes gas cartridges (model "СО"), which were replaced after weight gain (relative to initial) on 50 grams.
Other ways of determining the need to replace cartridges
The documents[17][18] described Soviet cartridges (model "Г"), designed to protect from mercury. Their service life was limited to 100 hours of use (cartridges without particle filter), or 60 hours of use (cartridges with particle filter), after which it was necessary to replace the cartridges with a new one.
The documents[19][20] describe a non-destructive method of determining the remaining service life of used and new gas cartridges. The polluted air was pumped through the cartridge. The degree of purification of air depends on how much-unsaturated sorbent is in the cartridge. Therefore, accurate measurement of gas concentration in the cleaned air allows one to estimate the amount of the unsaturated sorbent. Polluted air (1-bromobutane) was pumped for a very short time, and therefore, such tests do not reduce the service life considerably. The sorption capacity decreased due to absorption of this gas by the amount of about 0.5% of the sorption capacity of a new cartridge. The method was also used for 100% quality control of cartridges, manufactured by the English firm Martindale Protection Co (10 microliters 1-bromobutane injected into the air stream), and to check the cartridges issued to workers in firms Waring Ltd and Rentokil Ltd. This method was used in the Chemical Defence Establishment in the early 1970s. The experts who developed this method, received a patent.[21]
The document[22] briefly describes two methods of objective evaluation of the degree of saturation of the sorbent in the cartridges. It recommends using spectral and microchemical methods. The spectral method is based on determining the presence of harmful substances in the cartridge by sampling with subsequent analysis on a special device (стилоскоп - on Russian). A microchemical method is based on a layer-by-layer determination of the presence of harmful substances in the sorbent by sampling with subsequent analysis by chemical method. If the air is contaminated with the most toxic substances, the book is recommended to limit the duration of use of the cartridges, and it recommended to apply the spectral method (arsine and phosphine, phosgene, fluorine, organochloride, organometallic compounds), and microchemical methods (hydrogen cyanide, cyanogens).
Unfortunately, in both cases, there is no description of how to extract a sample of the sorbent from the cartridge housing (the housing is usually not detachable), and will it be possible to use the cartridge after this test, if the test shows that it is not a lot of saturated sorbents.
Modern methods of determining the necessity of cartridges replacement
Cartridges certification provides a minimum value of their sorption capacity. US OSHA standard for 1,3-Butadiene indicates the specific service life of the cartridges.[23]
Testing the cartridges in a laboratory
If the company has a laboratory that has the right equipment, specialists can skip the contaminated air through the cartridge and to determine a degree of it cleaning. This method enables one to determine the service life in an environment where the air is contaminated with a mixture of different substances that affect their capture with a sorbent (one affects on another capture). Service life calculation methods for such conditions have been developed relatively recently. However, this requires accurate information on concentrations of noxious substances, and they often are not permanent.
Tests in laboratories can identify what is the balance of the service life of the cartridges after their use. If the remainder is large, similar cartridges in such circumstances can be used over a longer period of time. In some cases, large balance allows the use of cartridges repeatedly. This method does not require accurate information on concentrations of harmful substances. The cartridge replacement schedule is drawn upon the basis of the results of their testing in the laboratory. This method has a serious drawback. The company must have a complex and expensive equipment and trained professionals (for using it) - is not always possible. According to a poll,[24] cartridges replacement in the United States was carried out on the basis of their laboratory tests on approximately 5% of all organizations.
Research to determine whether it is possible to calculate the service life of respirator's cartridges (if one know the conditions of their use) have been conducted in developed countries since the 1970s. This allows one to replace cartridges in a timely fashion - without the use of sophisticated and expensive equipment.
Computer programs for calculating the service life of the cartridge
The world's leading manufacturers of respirators offered its customers a computer program for calculating the service life already in the 2000.
Programs to determine the lifetime of the cartridges;[25] original[26] (in 2000). | ||||||
---|---|---|---|---|---|---|
Manufacturer of RPD | Program name | Number of substances (in 2000) | Types of gases and vapors | The range of polluted air temperatures, °С | Relative humidity, % | Air flow, l/min |
AO Safety | Merlin[27] | 227 | organic and inorganic | 0-50 | <50, 50-65, 65-80, 80-90 | light, medium and heavy work |
3М | 3M Service Life Software[28] | 405 (more than 900 in 2013) | organic and inorganic | 0, 10, 20, 30, 40, 50 | <65, >65 | 20, 40, 60 |
MSA | MSA — Cartridge Life Calculator[29] | 169 | organic and inorganic | freely chosen | 0 - 100 | 30, 60, 85 |
North | ezGuide v. 1.0[30] | 176 | organic and inorganic | freely chosen | <65, 66-80, >80 | 30, 50, 70 |
Survivair | Respirator Cartridge Service Life Program[31] | 189 | organic and inorganic | from -7 to +70 | <65, 66-80, >80 | 30, 50, 70 |
3M program[28] allowed to calculate the service life of the cartridges exposed with more than 900 harmful gases and their combinations (in 2013). The MSA program[29] allow to take into account hundreds of gases and their combinations. Same program was developed by Scott[32] and Dragerwerk.[33] J. Wood developed a mathematical model and software which now allows one to calculate the service life of any cartridges with known properties.[34][35] Now OSHA uses it in program Advisor Genius.[36]
The merit of this way of replacing the cartridges is that it allows an employer to use normal, "common" cartridges, and if they have the exact data, they may replace them in time. The downside is that because of air contamination is often not constant, and the nature of the work to be performed is not always stable (that is, the flow of air through the cartridges is not permanent), it is recommended to use working conditions for calculations, equal to the worst (for reliable protection of workers). But in all other cases, cartridges will be replaced with a partially used sorbent. This increases the costs of respiratory protection due to more frequent cartridges replacement.
In addition, calculation accuracy is reduced when very high relative humidity, because the mathematical model does not take into account some of the physical effects in such cases.
End of service life indicators (ESLI)

If the cartridges have a device that warns of an employee of the approaching expiration of the term of service life (End of Service Life Indicators, ESLI), the signals of such devices can be used for the timely replacement of cartridges. ESLI can be active[37] or passive.[38] Passive indicators often use sensor that changes color. This element is installed in the cartridge at some distance from the filtered air outlet (to color change occurred before the harmful gases begin to pass through the cartridge). An active indicator is used as a signal from a sensor to emit a light signal (or turn on a sound alarm) to inform an employee that he or she must leave the contaminated atmosphere and change the cartridge.
Active indicators used light or audible alarm for employee notification that is triggered by a sensor, that is usually installed in the cartridge. Such indicators allow one to replace the cartridges on time in any light and do not require the worker to pay attention to the color of the indicator. They can also be used by workers who badly distinguish different colors.
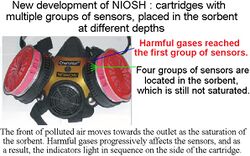
Despite the presence of solutions for technical problems, and the availability of the established certification requirements to the ESLI,[40] during the period from 1984 (first certification standard with requirements for active ESLI) until 2013 nor one cartridge with active ESLI was approved in the US. It turned out that the requirements for the cartridges are not quite exact, and requirements for employers are under no obligation to use these indicators quite specifically. Therefore, respirators’ manufacturers fear of commercial failure when selling new unusual products - although they continue to carry out research and development work in this area.

But examination of the use of respirators showed that in the U.S. more than 200 thousand workers may be exposed to excessive harmful gases due to the late replacement of cartridges.[24] So, Laboratory of PPE (NPPTL) at the NIOSH began to develop an active ESLI. After the completion of the work, by its results, the legal requirements will be clarified, the requirements of the employer will be formulated, and the resulting technology will be transferred to industry - for use in new improved RPD.[38]
Reusing cartridges
If the cartridge contains a lot of the sorbent and if the concentration of contaminants is low; or if the cartridge was used for a short duration of time, after completion of its use, it still has a lot unsaturated sorbent (which can capture gases). This may allow using such cartridges again.
The molecules of an entrapped gases may de-absorb during storage of the cartridge. Due to the difference of concentrations inside the body of the cartridge (at the inlet concentration is greater; at the outlet for purified air concentration is lesser), these de-absorbed molecules migrate inside the cartridge to the outlet. The study of cartridges exposed to methyl bromide showed that this migration can impede the re-use of storage.[42] The concentration of harmful substances in the purified air may exceed the PEL (even if clean air is pumped through the cartridge). To protect workers ' health, U.S. law does not allow reuse cartridges, when exposed to harmful substances, which are able to migrate (even if the cartridge has much non-saturated sorbent after the first use). According to the standards, "volatile" substances (able to migrate) are considered substances with a boiling point below 65 °C. But studies have shown that at the boiling point above 65 °C the reuse of the cartridge may be unsafe. Therefore, the manufacturer must provide the buyer with all the information required for the safe use of cartridges. So, if the period of a continuous service life of the cartridge (calculated by the program - see above) exceeds 8 hours (tables 4 and 5), the legislation may limit their use to one shift.
The paper [43] provides a procedure for calculating the concentration of harmful substances in the purified air at the start of the re-use of cartridges (which allows one to determine exactly where they may be safely reused). But these scientific results are not yet reflected in any standards or guidelines on the use of respirators. The author of the article, working in the US, did not even try to consider the use of gas cartridges for the third time (or more). On the website of the author, one can download for free a computer program that allows one to calculate the concentration of harmful substances immediately after the start of re-use of the cartridge (which allows one to determine if this is safe).[35]
Regeneration gas cartridges
Molecules of harmful gases adsorbed by activated carbon, do not form strong bonds with them and can de-absorb. Some harmful gases react with the sorbent and form strong bonds. Special technologies have been developed for the recovery of used cartridges. They created conditions that have stimulated de-sorption caught earlier harmful substances. This used steam or heated air in the 1930s [44][45] or other methods.[46] Processing of the sorbent was carried out after its removal from the body of the cartridge, or without removing.
Specialists tried to use as the absorber ion-exchange resin in 1967. The authors proposed to regenerate the sorbent by washing it in a solution of alkali or soda.[47]
The study[42] also showed that cartridges can be effectively regenerated after exposure to methyl bromide (when they are blowing with hot air 100÷110 °C, flow rate 20 l/min, duration about 60 minutes).
The regeneration of sorbents used consistently and systematically in the chemical industry, as it allows one to save money on the replacement of the sorbent, and as the regeneration of industrial gas cleaning devices can be carried out thoroughly and in an organized manner. But in the mass use of gas masks by different people in different conditions it is impossible to control the accuracy and correctness such regeneration of respirators’ cartridges. Therefore, despite the technical feasibility and commercial benefits, regeneration of respirators’ cartridges is not carried out.
Legal requirements for the timely replacement of respirator's cartridges
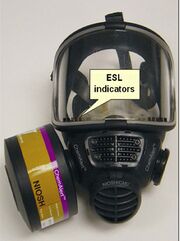

Since it is not always possible to replace cartridges in a timely manner through the use of their odor ets,[clarification needed] OSHA has banned the use of this method. The employer is obliged to use only two ways to replace cartridges:[48] on schedule, and by using ESLI (because only these methods provide reliable preservation of workers’ health). Instructions to inspectors (OSHA) provides specific guidance on inspection of implementation of such requirements.[49] On the other hand, the state requires manufacturers to provide the consumer with all the necessary information about cartridges, that allows one to make a schedule for replacing them timely. Similar requirements exist in the standard on occupational safety, governing the selection and application of RPD in EU.[50] In England a tutorial on the selection and use of respirators recommends obtain information from the manufacturer, and replace the cartridges on a schedule, or use ESLI, and prohibits reuse cartridges after exposure of volatile substances that can migrate.[51]
- The US law required the employer to use exceptionally supplied air RPD (SAR) for protection against harmful gases, that have no warning properties.[48][52] The use of supplied air respirators may be the only way to reliably protect workers in circumstances when there is no ESLI, and it is impossible to calculate the service life.
- Legislation in the EU[53][54] allows an employer to use of only an supplied air respirators when employee works in conditions where air pollution is IDLH (because of the risk of not timely replacement of cartridges).
References
- ↑ (>19.5% in US; >18% in RF)
- ↑ David S. DeCamp, Joseph Costantino, Jon E. Black (November 2004) (in en). Estimating Organic Vapor Cartridge Service Life. Kennedy Circle Brooks City-Base: Air Force Institute for Operational Health Risk Analysis Directorate. pp. 53. https://apps.dtic.mil/dtic/tr/fulltext/u2/a439710.pdf. Retrieved 9 November 2019.
- ↑ Jump up to: 3.0 3.1 Дубинин, Михаил; Чмутов К. (1939) (in ru). Физико-химические основы противогазного дела // Physico-chemical bases of development and application of gas masks. Moscow: Военная академия химической защиты имени К.Е. Ворошилова.
- ↑ Clayton G.D.; Clayton E.F (1985). Patty's Industrial Hygiene and Toxicology. 1 (3 ed.). New York: Willey-Interscience. p. 1008. ISBN 978-0-471-01280-1.
- ↑ 42 Code of Federal Register 84 Approval of respiratory protective devices §84.113 — Canisters and cartridges; color and markings; requirements
- ↑ Rosenstock, Linda (1999). "Appendix A". TB Respiratory Protection Program In Health Care Facilities. DHHS (NIOSH) Publication No. 99-143. Cincinnati, Ohio: National Institute for Occupational Safety and Health. pp. 42–44. https://www.cdc.gov/niosh/docs/99-143/.
- ↑ RF state standard ГОСТ Р 12.4.193-99 Occupational safety standards system. Respiratory protective devices. Gas filters and combined filters. General specifications (on Russian)
- ↑ RF state standard ГОСТ Р 12.4.231-2007 Occupational safety standards system. Respiratory protective devices. АX gas filters and combined filters for protection against low-boiling organic compounds. General specifications (on Russian)
- ↑ RF state standard ГОСТ Р 12.4.232-2007 Occupational safety standards system. Respiratory protective devices. SX gas filters and combined filters for protection against specific named compounds. General specifications (on Russian)
- ↑ RF state standard ГОСТ 12.4.235-2012 (EN 14387:2008) Occupational safety standards system. Respiratory protective devices. Gas filters and combined filters. General technical requirements. Test methods. Marking (on Russian)
- ↑ RF state standard ГОСТ 12.4.245-2013 Occupational safety standards system. Respiratory protective devices. Gas filters and combined filters. General specifications (on Russian)
- ↑ Michael E. Barsan, ed (2007). NIOSH Pocket guide to chemical hazards. DHHS (NIOSH) Publication No. 2005-149 (3 ed.). Cincinnati, Ohio: National Institute for Occupational Safety and Health. pp. xiv–xvi; xx–xxiii; 2–340. https://www.cdc.gov/niosh/docs/2005-149/.
- ↑ Jump up to: 13.0 13.1 13.2 Bollinger, Nancy (October 2004). NIOSH Respirator Selection Logic. NIOSH-Issued Publications. Cincinnati, OH: National Institute for Occupational Safety and Health. doi:10.26616/NIOSHPUB2005100. https://www.cdc.gov/niosh/docs/2005-100/.
- ↑ 2008 Respirator Selection Guide. St. Paul, MN: 3M. 2008. pp. 15–96.
- ↑ Myers, Warren (1987). "Appendice C. Odor warning: Background information.". in Donald Miller. NIOSH Respirator Decision Logic. DHHS (NIOSH) Publication No. 87-108. Cincinnati, Ohio: National Institute for Occupational Safety and Health. pp. 48–50. https://www.cdc.gov/niosh/docs/87-108/.
- ↑ Amoore, John; Hautala Earl (1983). "Odor as an aid to chemical safety: odor thresholds compared with threshold limit values and volatilities for 214 industrial chemicals in air and water dilution". Journal of Applied Toxicology 3 (6): 272–290. doi:10.1002/jat.2550030603. ISSN 1099-1263.
- ↑ Jump up to: 17.0 17.1 Трумпайц Я.И.; Афанасьева Е.Н. (1962) (in ru). Индивидуальные средства защиты органов дыхания (альбом) // Respiratory Protective Devices (album-catalogue). Leningrad: Профиздат.
- ↑ Шкрабо М.Л. (1982) (in ru). Промышленные противогазы и респираторы. Каталог. // Industrial Respiratory Protective Devices. Catalogue.. Cherkassy: Отделение НИИТЭХИМа.
- ↑ Maggs F.A.P (1972). "A Non-destructive Test of Vapour Filters" (in en). The Annual of Occupational Hygiene 15 (2–4): 351–359. doi:10.1093/annhyg/15.2-4.351. ISSN 1475-3162. PMID 4648247. http://annhyg.oxfordjournals.org/content/15/2-4.toc.
- ↑ Ballantyne, Bryan et al. (1981) (in en). Respiratory Protection. Principles and Applications. London, New York: Chapman & Hall. ISBN 978-0412227509.
- ↑ British Patent No 60224/69
- ↑ Тихова Т.С.. Капцов В.А.. ed (in ru). Средства индивидуальной защиты работающих на железнодорожном транспорте. Каталог-справочник // Personal protective equipment for railway workers. Сatalogue-guidebook. Moscow: ВНИИЖГ, Транспорт. p. 245.
- ↑ US OSHA occupational health and safety standard 29 Code of Federal Register 1910.1051 1,3-Butadiene 1910.1051(h)(3) Respirator selection
- ↑ Jump up to: 24.0 24.1 U.S. Department of Labor, Bureau of Labor Statistics (2003). Respirator Usage in Private Sector Firms. Morgantown, WV: U.S. Department of Health and Human Services, Centers for Disease Control and Prevention, National Institute for Occupational Safety and Health. pp. 214 (table 91). https://www.cdc.gov/niosh/docs/respsurv/pdfs/respsurv2001.pdf.
- ↑ ZieglerG., Martin; Hauthal W.; Koser H. (2003) (in de). Entwicklung von Indikatoren zur Anzeige des Gebrauchsdauer-Endes von Gasfiltern (Machbarkeitsstudie). Forschung Fb 997 (1 ed.). Bremerhaven: Wirtschaftsverl. ISBN 978-3-86509-041-6.
- ↑ Cothran T. (2000). "Features - Service Life Software for Organic Vapour Cartridges". Occupational Health and Safety 69 (5): 84–93. ISSN 0362-4064.
- ↑ The link to the document describing the program MerlinTM . Unfortunately, the product could not be found.
- ↑ Jump up to: 28.0 28.1 3M Service Life Software Version: 3.3 until January 1, 2016.
- ↑ Jump up to: 29.0 29.1 MSA program Cartridge Life Calculator link 1 link 2 (for US)
- ↑ Old link: Program for Cartridge Service Life calculation ezGuide
- ↑ Link to the manufacturer's website where You can download a program to calculate the life of the cartridges: S-Series - Software Downloads and T-Series - Software Downloads.
- ↑ The program for calculation of service life of respirator cartridges, developed by Scott: SureLife™ Cartridge Calculator
- ↑ Link to a database VOICE developed by Drager (version for US) with the program for calculation cartridge service life End-of-ServiceLife Calculator
- ↑ Wood, Gerry; Jay Snyder (2007). "Estimating Service Lives of Organic Vapor Cartridges III: Multiple Vapors at All Humidities". Journal of Occupational and Environmental Hygiene 4 (5): 363–374. doi:10.1080/15459620701277468. ISSN 1545-9632. PMID 17454504. https://zenodo.org/record/1234513.
- ↑ Jump up to: 35.0 35.1 Computer program "MultiVapor with IBUR" - Immediate Breakthrough Upon Reuse
- ↑ The program for calculation of service life of respirator cartridges that use a mathematical model of Jerry Wood: Advisor Genius
- ↑ Rose-Pehrsson, Susan L.; Williams, Monica L. (2005). Integration of Sensor Technologies into Respirator Vapor Cartridges as End-of-Service-Life Indicators: Literature and Manufacturer's Review and Research Roadmap. Washington, DC: US Naval Research Laboratory. p. 37. http://oai.dtic.mil/oai/oai?verb=getRecord&metadataPrefix=html&identifier=ADA434905. Retrieved 2015-06-27.
- ↑ Jump up to: 38.0 38.1 Favas, George (July 2005). End of Service Life Indicator (ESLI) for Respirator Cartridges. Part I: Literature Review. Victoria 3207 Australia: Human Protection & Performance Division, Defence Science and Technology Organisation. p. 49. http://www.dtic.mil/cgi-bin/GetTRDoc?Location=U2&doc=GetTRDoc.pdf&AD=ADA446250.
- ↑ Jump up to: 39.0 39.1 39.2 NPPTL presentation (2007) Sensor Development for ESLI & Application to Chemical Detection
- ↑ US NIOSH occupational safety and health standard 42 Code of Federal Register 84 Approval of Respiratory Protective Devices ‘’84.255 Requirements for end-of-service-life indicator.‘’
- ↑ Melissa Checky, Kevin Frankel, Denise Goddard, Erik Johnson, J. Christopher Thomas, Maria Zelinsky & Cassidy Javner (2016). "Evaluation of a passive optical based end of service life indicator (ESLI) for organic vapor respirator cartridges" (in en). Journal of Occupational and Environmental Hygiene 13 (2): 112–120. doi:10.1080/15459624.2015.1091956. ISSN 1545-9624. PMID 26418577. PMC 4720034. https://www.tandfonline.com/toc/uoeh20/13/2. Retrieved 10 June 2018. (Open access)
- ↑ Jump up to: 42.0 42.1 Maggs, F. A. P.; Smith, M. E. (1975). "The Use and Regeneration of Type-O Canisters for Protection Against Methyl Bromide". Annals of Occupational Hygiene 18 (2): 111–119. doi:10.1093/annhyg/18.2.111. ISSN 0003-4878. PMID 1059379.
- ↑ Wood, Gerry O.; Snyder, Jay L. (2011). "Estimating Reusability of Organic Air-Purifying Respirator Cartridges". Journal of Occupational and Environmental Hygiene 8 (10): 609–617. doi:10.1080/15459624.2011.606536. ISSN 1545-9624. PMID 21936700.
- ↑ Торопов, Сергей (1938) (in ru). Испытания промышленных фильтрующих противогазов // The testing of industrial air purifying respirators. Moscow: Государственное научно-техническое издательство технической литературы НКТП. Редакция химической литературы.
- ↑ Торопов, Сергей (1940) (in ru). Промышленные противогазы и респираторы // Industrial gas masks and respirators. Moscow Leningrad: Государственное научно-техническое издательство технической литературы.
- ↑ Руфф ВТ (1936). "Регенерация промышленных фильтрующих противогазов // Regeneration of cartridges from industrial RPD" (in ru). Гигиена труда и техника безопасности // Occupational Health and Safety (1): 56–60.
- ↑ Вулих А.И.; Богатырёв В.Л.; Загорская М.К.; Шивандронов Ю.А. (1967). "Иониты в качестве поглотителей для противогазов // The ion exchangers as a sorbent for respirator cartridges" (in ru). Безопасность труда в промышленности // Occupational Safety in Industry (1): 46–48. ISSN 0409-2961.
- ↑ Jump up to: 48.0 48.1 US OSHA occupational safety and health standard 29 Code of Federal Register 1910.134 Respiratory Protection
- ↑ Charles Jeffress (OSHA) Instruction CPL 2-0.120 (1998)
- ↑ EN 529-2005 Respiratory protective devices - Recommendations for selection, use, care and maintenance - Guidance document
- ↑ HSE (2013). Respiratory protective equipment at work. A practical guide (4 ed.). Health and Safety Executive. ISBN 978-0-7176-6454-2. http://www.hse.gov.uk/Pubns/priced/hsg53.pdf.
- ↑ Bollinger, Nancy et al. (1987). A Guide to Industrial Respiratory Protection. NIOSH-Issued Publications. Cincinnati, OH: National Institute for Occupational Safety and Health. doi:10.26616/NIOSHPUB87116. https://www.cdc.gov/niosh/docs/87-116/.
- ↑ BS 4275:1997 Guide to implementing an effective respiratory protective device programme
- ↑ DIN EN 529:2006. Atemschutzgerate - Empfehlungen fur Auswahl, Einsatz, Pflege und Instandhaltung.